2024 نویسنده: Howard Calhoun | [email protected]. آخرین اصلاح شده: 2023-12-17 10:25
ریخته گری در قالب های صدفی را ریخته گری پوسته نیز می گویند. و در خارج از کشور به این روش کار شل می گویند.
اطلاعات عمومی
در صنعت صنعتی امروزی از روش های مختلف ریخته گری استفاده می شود. علاوه بر ریخته گری پوسته، ریخته گری سرمایه گذاری نیز استفاده می شود و همچنین در قالب های فلزی و چندین روش دیگر. مزیت کلی این روشهای ریختهگری در مقایسه با قالبگیری شن و ماسه، این است که مواد نهایی دقیقتری از نظر شکل و همچنین ابعاد به دست میآیند. علاوه بر این، تعداد ناهمواری های سطح چنین محصولاتی کاهش می یابد. در موارد نادرتر، اما همچنان اتفاق می افتد که نیاز به ماشینکاری بعدی پس از ذوب برطرف می شود. علاوه بر همه چیز، استفاده از ریخته گری در قالب های پوسته و سایر روش ها به مکانیزه شدن این فرآیند تا حد امکان کمک می کند که در نتیجه اتوماسیون آن نیز افزایش می یابد. و این، البته، بهره وری هر تاسیسات صنعتی را تا حد زیادی افزایش می دهد.
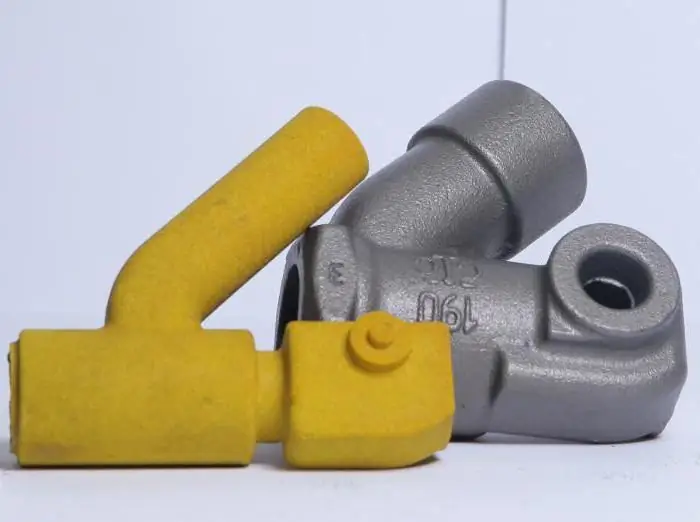
بازیگران پوسته
اگر به طور خاص در این مورد صحبت کنیمروش، اولین بار در سال 1953 در کارخانه ها معرفی شد. در حال حاضر، این روش به طور گسترده ای استفاده می شود. برای مثال، ریخته گری در قالب های پوسته ای است که بیشتر قطعات تراکتور کیروتس را تولید می کند. تمامی قطعاتی که با این روش تولید می شوند از فولاد یا چدن با بالاترین کیفیت می باشند. ریخته گری پوسته ای روشی است که در آن نتیجه نهایی ریخته گری به شکلی متشکل از دو پوسته رزین ماسه ای است. همچنین این روش ساخت قطعات تنها در مواردی مورد استفاده قرار می گیرد که لازم باشد قطعه ای با ابعاد کوچک یا متوسط و در عین حال با دقت بالا ایجاد شود. نمونه هایی از کاربردهای این روش ریخته گری قطعات موتور یا ریخته گری دیواره نازک است.
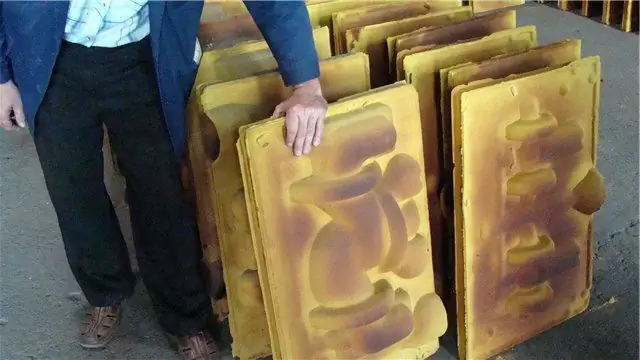
جوهر راه
با این روش کار می توانید قطعات مختلفی برای فن، موتور، پمپ یا ماشین آلات نساجی تهیه کنید. با این حال، حداکثر طول محصول دریافتی نمی تواند از 1 متر تجاوز کند و نمی تواند سنگین تر از 200 کیلوگرم باشد.
ماهیت ریختهگری در قالبهای پوسته بر اساس ویژگیهای خاصی از رزینهای ترموست است که بخشی از مخلوطهای شن و رزین هستند. مزیت استفاده از چنین اجزای این است که این رزین ها در دمای 200 تا 250 درجه سانتیگراد به سرعت و به طور دائم سفت می شوند.
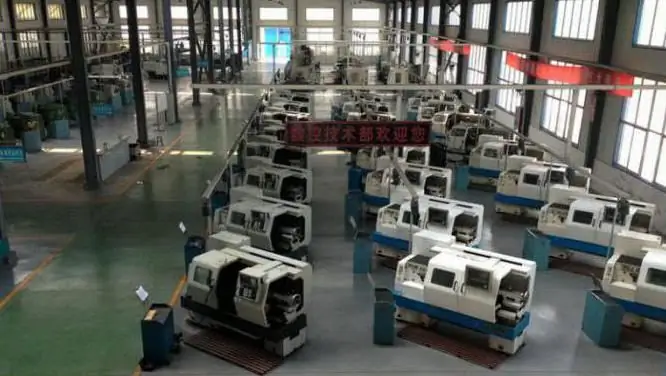
ساخت قالب صدفی برای ریخته گری
برای ساخت قالب برای ریخته گری بعدی، باید ماسه کوارتز ریزدانه داشته باشیم که همراه با افزودن یک رزین ترموست که عنصر اتصال آن برای به دست آوردن یک قالب پوسته کامل است، می باشد. این مواد، به ویژه رزین، به این دلیل انتخاب می شوند که وقتی از مانع دمایی خاصی عبور می کنند، سخت می شوند. فرآیند تولید به شرح زیر است. ابتدا رزین تا 140-160 درجه سانتیگراد گرم می شود. تحت تأثیر چنین محیطی به یک توده چسب مایع تبدیل می شود که کاملاً قالب ماسه کوارتز را می پوشاند.
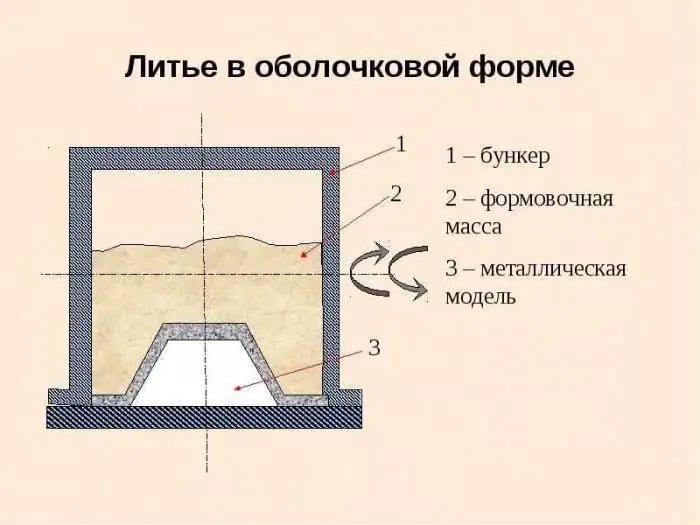
دامنه ریختهگری در قالبهای پوستهای بسیار گسترده است، بنابراین فرآیند ساخت قالبها به صورت خودکار یا خودکار انجام میشود.
پس از پوشاندن کامل قالب با رزین، دما را به 200-250 درجه سانتیگراد افزایش می دهند. این آستانه دما کاملاً کافی است تا جرم چسب به طور برگشت ناپذیر سخت شود و شکلی به خود بگیرد. علاوه بر این، زمانی که فرآیند ریختهگری قطعات آغاز میشود، یعنی زمانی که فلز مذاب وارد قالب میشود، دمای آن به حدود 600 درجه میرسد. این حالت کافی است تا اطمینان حاصل شود که رزین ذوب نمی شود، بلکه می سوزد، در حالی که منافذ را روی قالب باقی می گذارد و خروج گازها را تسهیل می کند.
مزایا و معایب ریخته گری قالب پوسته
مانند هر فرآیند تولید دیگری، این یکی نیز مزایا و معایب خود را دارد. اگر این روش ریخته گری را مثلا با ریخته گری مقایسه کنیمقالب های شن و ماسه معمولی چندین مزیت دارد:
- اولین و نسبتاً مهم تفاوت در کلاس دقت است که 7-9 است. علاوه بر این، پرداخت سطح قطعه به دست آمده تا 3-6 بهبود می یابد. علاوه بر این، هزینه ها کاهش می یابد، که برای ماشینکاری بعدی قسمت حاصل پس از ریخته گری مجاز است.
- یکی از مزیت های بزرگ کاهش قابل توجه هزینه های نیروی کار برای ساخت قطعات ریخته گری است.
- این روش ریخته گری به دلیل کاهش اندازه کانال های دروازه، مصرف مواد قالب گیری و همچنین مقدار فلز را کاهش می دهد.
- به طور قابل توجهی میزان خروجی ازدواج را کاهش داد.
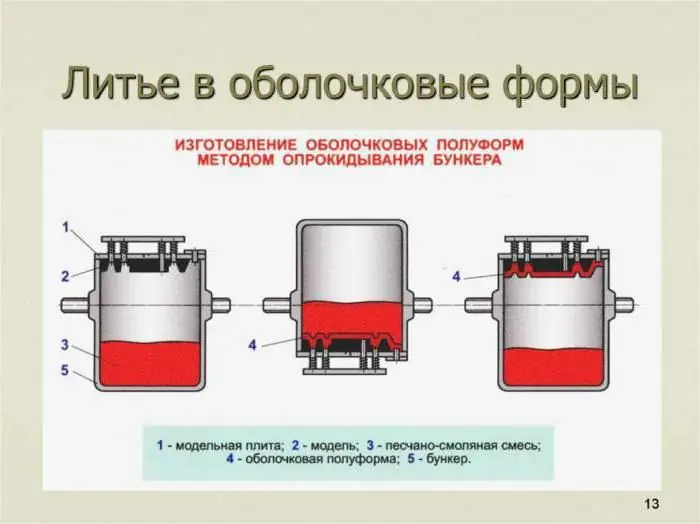
با این حال، برخی از معایب ریخته گری در قالب های پوسته ای وجود دارد. این موارد عبارتند از:
- دوام قالب پوسته - 1 ریخته گری.
- هزینه قالب گیری شن و ماسه بسیار بالا است.
- درصد بالای گازهای مضر.
فرایند تشکیل پیکره
فرایند شکل گیری بدن در شش مرحله انجام می شود:
- مرحله اول، فرآیند ریختن مخلوط روی یک مدل فلزی داغ و همچنین فرآیند نگهداری آن برای چند ده ثانیه است تا زمانی که یک پوسته نازک و قوی در اطراف قطعه ایجاد شود. اغلب مدل ها از چدن ساخته می شوند و حرارت آنها تا 230-315 درجه انجام می شود.
- بعد از آن لازم است عملیات حذف ماسه قالب گیری اضافی انجام شود. ضخامت پوسته در نهایت باید از 10 تا 20 باشدمیلی متر این به زمان ماندگاری مخلوط روی مدل و همچنین به دما بستگی دارد.
- بعد از آن لازم است صفحه مدل را به همراه قالب به فر منتقل کنید تا تا پایان عمل آوری در آنجا باشند. در پایان این روش، استحکام پوسته باید بین 2.4 تا 3.1 مگاپاسکال باشد.
- پس از خارج شدن از کوره، پوسته سخت شده از صفحه خارج می شود. یک فشار دهنده مخصوص برای این روش استفاده می شود.
- پس از آن، دو یا چند مدل با استفاده از نوعی گیره یا با چسب زدن به یکدیگر محکم می شوند. این قالب ها را می توان برای ریخته گری در قالب های پوسته ای استفاده کرد یا به سادگی ذخیره کرد. ماندگاری تقریبا نامحدود.
- قبل از شروع فرآیند ریخته گری در قالب تمام شده، گلوله در آنها ریخته می شود که به جلوگیری یا از بین بردن قالب در هنگام ریختن بیشتر کمک می کند.
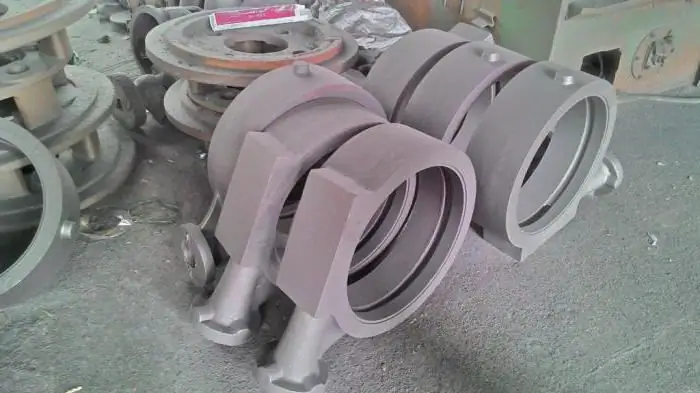
جزئیات بازیگری
ارزش دارد با این واقعیت شروع کنیم که تلورانس های معمولی که در ساخت ابزارآلات مجاز هستند می تواند 0.5 میلی متر باشد. زبری سطح در محدوده 0.3 تا 0.4 میکرون مجاز است. چنین محدودیت هایی با این واقعیت توجیه می شود که از ماسه ریز دانه استفاده می شود. همچنین شایان ذکر است: استفاده از رزین تا حد زیادی به این واقعیت کمک می کند که سطح بسیار صاف باشد.
حجم تولید
برای پرداختن به تولید این گونه قالب ها و قطعات باید به نصب مدل قالب توجه کرد. زمان لازم برای نصب کمتر از یک هفته است. پس از اتمام نصب، مقدار خروجی می توانداز 5 تا 50 قطعه در ساعت می رسد. چنین حجم تولید در ساعت کاملاً واقعی است، با این حال، برای این امر لازم است فرآیند ریخته گری بر این اساس آماده شود. مواد اصلی که برای ریخته گری مورد نیاز خواهد بود، چدن، آلومینیوم، مس و همچنین آلیاژهای این نوع فلزات می باشد. یکی دیگر از مواد ضروری آلیاژی است که از آلومینیوم و منیزیم استفاده می کند.
توصیه شده:
شاخص هایی برای پوسته پوسته شدن بدون ترسیم مجدد: ویژگی ها، مزایا و معایب
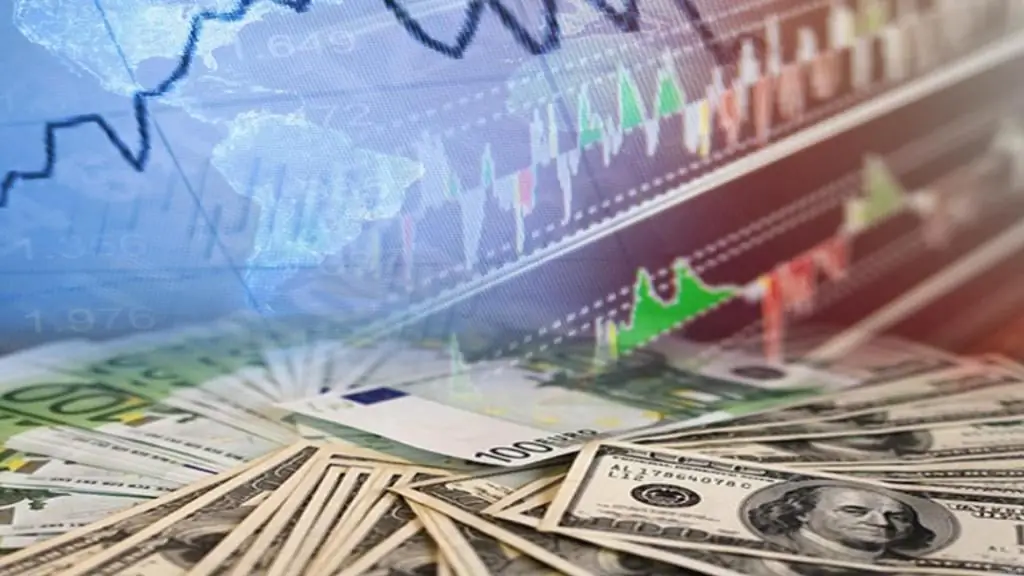
در معاملات در بازارهای مالی، روش های مختلفی وجود دارد که معامله گران از طریق آن کسب درآمد می کنند. هر سیستم معاملاتی ویژگی ها و ویژگی های خاص خود را دارد و اکثر آنها از ابزارهای خاصی استفاده می کنند. در این مقاله، خواننده با انواع مختلف ابزارهای معاملاتی، از جمله اندیکاتورهای "اسکالپینگ" بدون ترسیم مجدد آشنا می شود
ریخته گری مستمر فولاد: اصل عملیات، تجهیزات لازم، مزایا و معایب روش
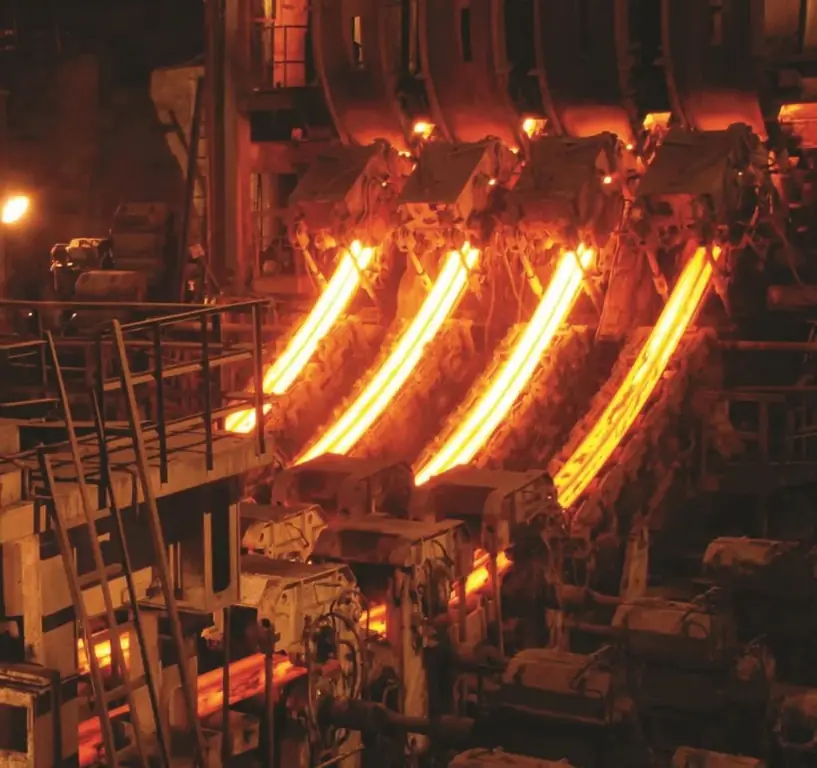
امروزه تعداد زیادی از چیزها، قطعات و غیره از فولاد ساخته می شود، طبیعتاً این نیاز به مقدار زیادی منبع دارد. بنابراین، گیاهان مدت طولانی است که از روش ریخته گری مداوم فولاد استفاده می کنند که با مهمترین ویژگی - بهره وری بالا مشخص می شود
ریخته گری در قالب سیلیکونی: تجهیزات. ریخته گری خلاء در قالب های سیلیکونی
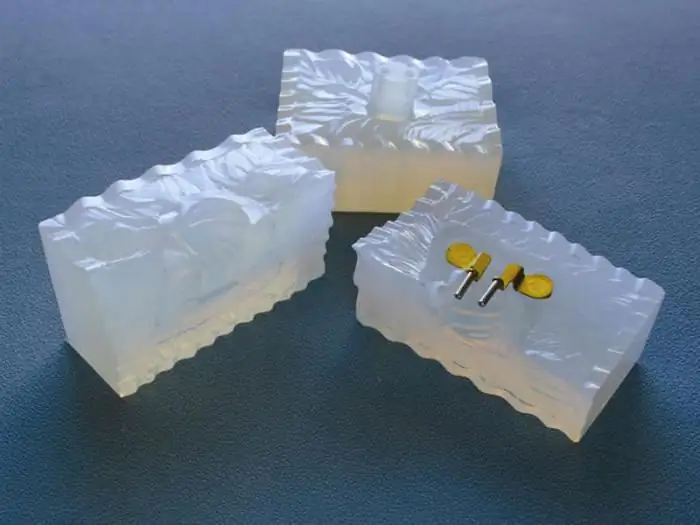
برای ساخت تعداد کمی از قطعات پلاستیکی، اغلب از ریخته گری با خلاء در قالب های سیلیکونی استفاده می شود. این روش کاملا مقرون به صرفه است (ساخت قالب فلزی به زمان و هزینه بیشتری نیاز دارد). علاوه بر این، قالب های سیلیکونی به طور مکرر استفاده می شود و این نیز هزینه تولید را به میزان قابل توجهی کاهش می دهد
قالب ریخته گری: ویژگی ها، فناوری، انواع
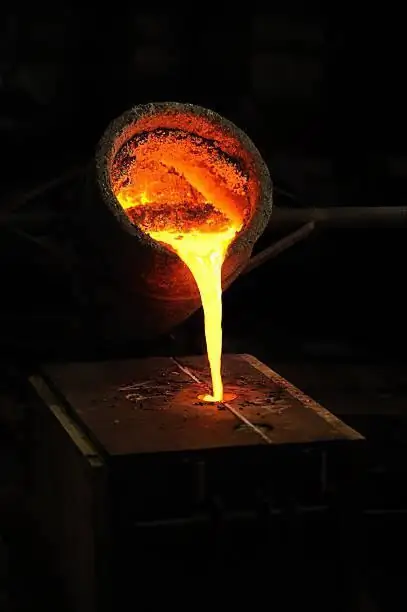
یکی از فرآیندهای مهم در صنعت، فرآیند ریخته گری انواع قطعات، مواد اولیه و موارد دیگر است. با این حال، برای تولید موفقیت آمیز چیز مورد نظر، لازم است قالبی برای آن ساخته شود که تا حد زیادی نتیجه نهایی را تعیین می کند
سیستم های دروازه: انواع، دستگاه. قالب ریخته گری
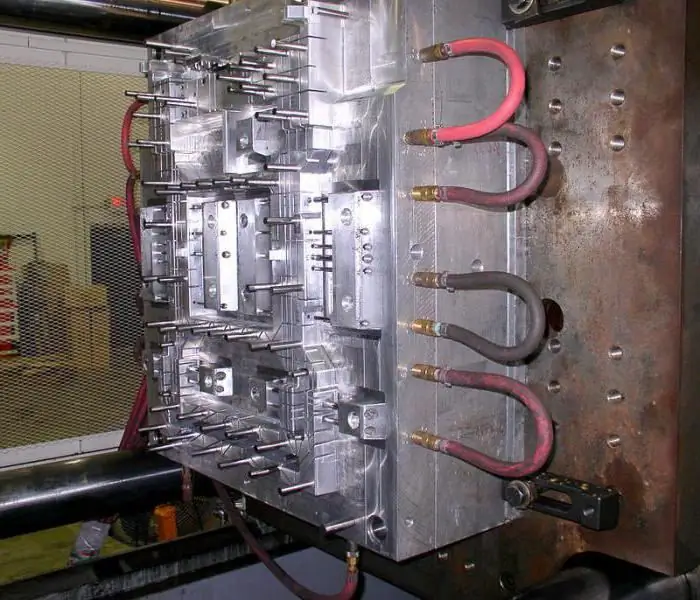
سیستم های دروازه ای: اصل عملکرد، توضیحات، ویژگی ها، دستگاه، عملیات. قالب برای ریخته گری: هدف، ویژگی ها، عکس