2024 نویسنده: Howard Calhoun | [email protected]. آخرین اصلاح شده: 2023-12-17 10:25
فناوری های جوشکاری و روکش بازیابی موثر قطعات فلزی را امکان پذیر می کند و درجه بالایی از قابلیت اطمینان و دوام محصول را فراهم می کند. این امر با استفاده از این روش ها هنگام انجام عملیات تعمیر در زمینه های مختلف - از تعمیرات خودرو گرفته تا تولید فلز نورد - تأیید می شود. در مجموع کار بر روی تعمیر سازه های فلزی، ترمیم قطعات با جوش و روکش حدود 60-70٪ طول می کشد. رایج ترین تعمیر بلوک سیلندر فولادی، میل موتور، میل لنگ، زنجیر، تیغه و …
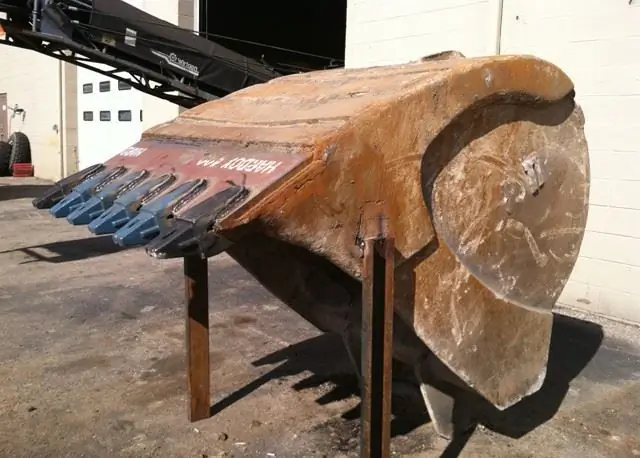
جوشکاری و روکش کاری در تعمیر و ترمیم
هر دو روش مبتنی بر روش های عملیات حرارتی با پارامترهای مختلف هستندعملکرد تجهیزات متصل جوشکاری فرآیند تشکیل پیوندهای بین اتمی است که می تواند برای اتصال عناصر مختلف یک قطعه، بستن شکاف های تکنولوژیکی و از بین بردن عیوب جزئی روی سطح استفاده شود. پتانسیل انرژی برای فرآیند جوشکاری با گرمایش عمومی یا موضعی قطعه کار تامین میشود.
عملیات معمولی از این نوع شامل تعمیر قطعات اضافی یا شکسته صفحات، رینگ ها و بوش ها است. علاوه بر تعمیر محصولات با اشکال هندسی ساده، کارهای مرمت پیچیده تر نیز امکان پذیر است، اما به عنوان بخشی از سایر عملیات های تکنولوژیکی. به عنوان مثال، ترمیم رزوه با جوشکاری با روش های صاف و تراش مکانیکی تکمیل می شود. علاوه بر این، در چنین کاری، الزامات گرم شدن بیش از حد ابزار کمکی مانند قالب ها، که مستقیماً در تصحیح رزوه نقش دارند، باید رعایت شود.
در مورد سطح بندی، این روش شامل اعمال یک پوشش فلزی اضافی بر روی سطحی است که قرار است بازسازی شود. لایه فناوری جدید می تواند هنگام تعمیر قطعات فرسوده یا تقویت سطح در ناحیه اصطکاک مفید باشد.
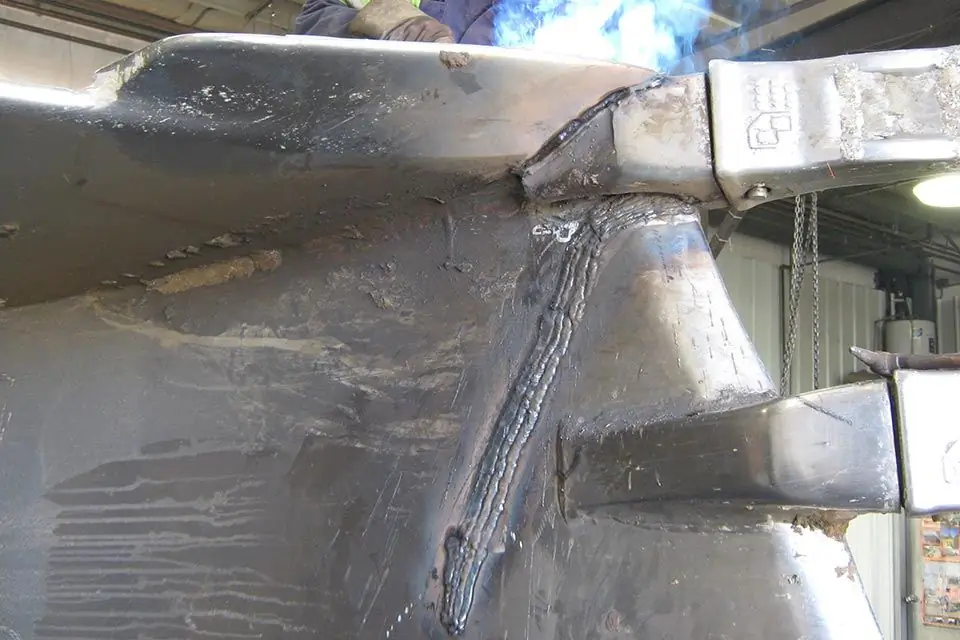
تجهیزات کاربردی
هنگام جوشکاری، لزوماً از یک منبع تغذیه، تجهیزاتی برای نگه داشتن قطعه و هدایت قوس استفاده می شود. بیشتر اوقات، از مبدل جوشکاری استفاده می شود که شامل یک موتور با ژنراتور DC از 70 تا 800 A است. می توان از یکسو کننده های ترانسفورماتور نیز استفاده کرد.دنده جریان و کنترل اگر در مورد مواد مصرفی و وسایل کمکی صحبت کنیم، ترمیم قطعات با جوش و روکش با اتصال دهانه های نگهدارنده، الکترودها و سیستم های خنک کننده انجام می شود. هنگام روکش کردن، از سرهای تغییر شکل با کولیس و بالابرها نیز استفاده می شود که امکان نصب بر روی ماشین ابزار (تراش یا برش پیچ) را می دهد. برش های ویژه برای حذف لبه ها و لایه های فلزی اضافی استفاده می شود.
شرایط آماده سازی قطعه
هم در جوشکاری و هم در فرآیند روکش، کیفیت عملیات تا حد زیادی با وضعیت اولیه قطعه کار تعیین می شود. سطوح قطعه باید از زنگ زدگی، رسوب، کثیفی و چربی تمیز شود. در غیر این صورت، خطر حفظ عدم نفوذ، ترک ها و آخال های سرباره افزایش می یابد. باید توجه ویژه ای به چربی زدایی از روغن های کارخانه ای و حفاظتی شود. این روش در محلول داغ انجام می شود و پس از آن محصول شسته و خشک می شود. قبل از ترمیم قطعات با جوشکاری، انجام سندبلاست توصیه می شود که کیفیت تعمیر را بهبود می بخشد. برای چنین کارهایی، از روش های پردازش ساینده با اتصال تجهیزات کمپرسور، دیسک های سنگ زنی و برش ها استفاده می شود. آثار خفیف آسیب خوردگی را نیز می توان با برس های فلزی دستی از بین برد.
کدام الکترودها برای بازیابی استفاده می شوند؟
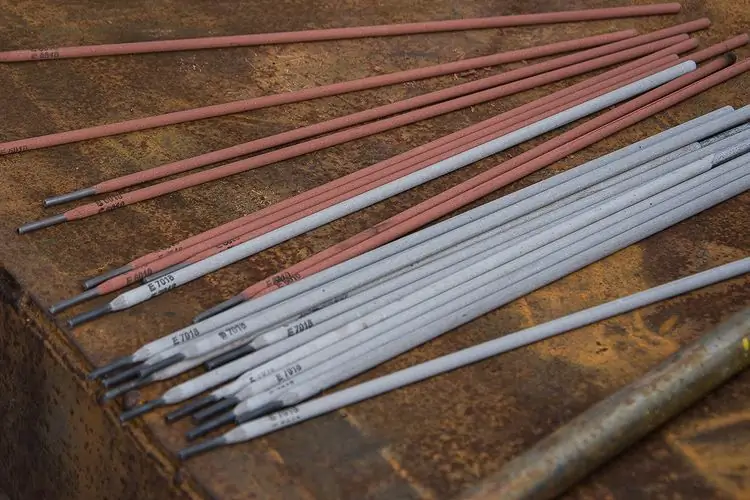
پس از تهیه تجهیزات اصلی کار و قطعه کار، می توانید به انتخاب الکترودها بروید. انتخاب بستگی به نوع فلز، ماهیت عیب والزامات برای لایه روکش به عنوان یک قاعده، در موارد رایج شکستگی ها و ترک ها، از الکترودهای جوشکاری معمولی با مقاومت کششی حدود 4 مگاپاسکال استفاده می شود. برای کار با فولادهای کربنی، استفاده از مواد مصرفی توصیه می شود که میله های آن از سیم گرید Sv-08 با ضخامت 1.5-12 میلی متر ساخته شده است. ویژگی های پوشش را نادیده نگیرید. اثر تثبیت کنندگی بالایی در ترمیم قطعات با جوش و روکش با پوشش گچی الکترود نوع E-34 ایجاد می شود. این به فرآیند سوزاندن قوس پایدار کمک می کند، که به شما امکان می دهد یک درز متراکم و یکنواخت ایجاد کنید.
مواد مصرفی الکترود غیر استاندارد مانند نوار و عناصر پودری لولهای نیز امروزه استفاده میشود. معمولاً آنها نوارهای فلزی تا ضخامت 0.8 میلی متر نورد می شوند که سطح آنها با مخلوط های آلیاژی پودری مختلف مبتنی بر فرومنگنز، استالینیت و غیره پر می شود. اگر برنامه ریزی شده است که منطقه تعمیر شده دارای خواص عملیاتی اضافی باشد، باید به چنین الکترودهایی پرداخت.
روش و روش جوشکاری قوس الکتریکی دستی
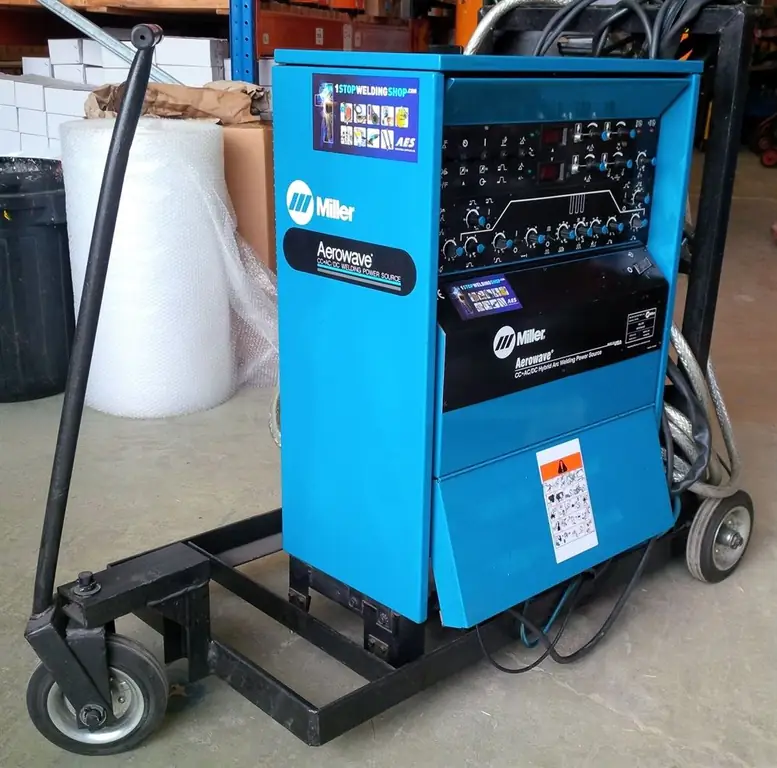
هنگام تعمیر جوش های آسیب دیده، آب بندی ترک ها و آب بندی موارد هرمتیک، می توانید از روش دستی با الکترودهای گرافیت، کربن یا تنگستن استفاده کنید. در حین کار، یک دسته میله با روکش گرفته می شود و با سیم بسته می شود. انتهای آن باید از قبل جوش داده شده و در نگهدارنده آماده شده قرار داده شود. در حین کار، الکترودها یک قوس به اصطلاح سرگردان با میدان عمل گسترده تشکیل می دهند. چگونههرچه ناحیه آسیب دیده بزرگتر باشد، پرتو باید بزرگتر باشد. مشکل اصلی فرآیند جوشکاری در این روش در نیاز به اتصال یک شبکه سه فاز نهفته است، زیرا همان سطح با پرتوی 5-6 الکترود باید با جریان افزایش یافته انجام شود. این روش برای تعمیر قطعات ساخته شده از فولادهای آلیاژی و کم آلیاژی با ضخامت متوسط و بزرگ استفاده می شود.
روش جوشکاری خودکار زیرپودری
فرایند روکش خودکار از این جهت متفاوت است که تامین الکترود با حرکت خود قوس در امتداد سطح کار کاملاً مکانیزه است. شار، به نوبه خود، ایزوله منطقه هدف را از اثرات مضر اکسیژن فراهم می کند. این روش برای ترمیم سطوح قطعات مسطح و استوانه ای با عمق سایش تا 15 میلی متر استفاده می شود. با افزایش اندازه عیب، می توان چندین لایه هارد فیسینگ را اعمال کرد، اما در این صورت باید منتظر پلیمریزاسیون هر لایه قبلی بود. این فناوری ترمیم قطعات با جوش و روکش مستلزم اتصال منابع جریان به صورت مبدل یا یکسو کننده با تراش پیچ برش است. یک پوشش شار به ضخامت 1-4 میلی متر در منطقه کار تشکیل می شود، پس از آن یک سیم الکترود با قوس به طور خودکار هدایت می شود. از مزایای اصلی این روش نسبت به جوشکاری دستی می توان به حداقل اتلاف فلز در نتیجه پاشش اشاره کرد. روش دستی چندین برابر خاکستر و ضایعات بیشتری می دهد.
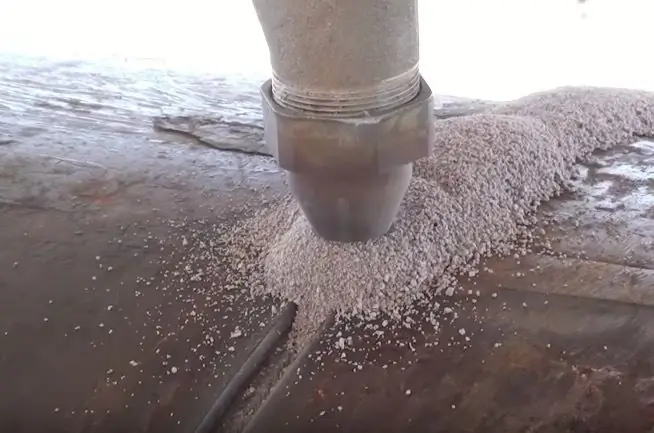
روش سطحی قوس ارتعاشی
در این مورد از الکترودهای همجوشی استفاده می شود که در این فرآیندقوس های سوزان با اتصال کوتاه به ارتعاش در می آیند. عملیات تامین و جابجایی مواد مصرفی نیز خودکار است. با وجود پیچیدگی بیرونی فرآیند، روش بسیار ساده است و نیازی به استفاده از تجهیزات خاصی ندارد. علاوه بر این، در دراز مدت، می توان انتظار حذف تغییر شکل قطعه با حفظ سختی بدون عملیات حرارتی را داشت. با این حال، محدودیت هایی نیز وجود دارد. بنابراین، روش های ارتعاشی برای بازیابی قطعات با جوش و روکش برای قطعات کار با قطر حداقل 8 میلی متر یا ضخامت 0.5 تا 3.5 میلی متر مناسب است. از نظر تئوری، سطح ارتعاشی قوس را می توان در محیط های حفاظتی مختلف با گاز یا شار انجام داد، اما در عمل بیشتر از عایق مایع استفاده می شود - به عنوان مثال، محلول خاکستر سودا.
جوشکاری و روکش در محیط های محافظ گاز
این روش شامل تهیه یک سیلندر مخصوص با مخلوط گاز فشرده است. گازهای آرگون و دی اکسید کربن را می توان استفاده کرد که تحت فشار بالا به ناحیه جوش هدایت می شوند. وظیفه مخلوط نیز به عملکرد محافظتی جداسازی قطعه کار از اثرات منفی نیتروژن و اکسیژن در هوا کاهش می یابد. بالاترین کیفیت اتصالات با جوشکاری در محیط های گازی با استفاده از الکترودهای تنگستن با ورودی جداگانه مواد پرکننده در ناحیه کار به دست می آید. سطح بندی تحت جریان مستقیم با قطبیت معکوس انجام می شود. اگر از سیم الکترود استفاده شود، میتوان فرآیند را مکانیزه کرد، اما مشعلهای گاز-الکتریک معمولاً به صورت دستی کار میکنند.
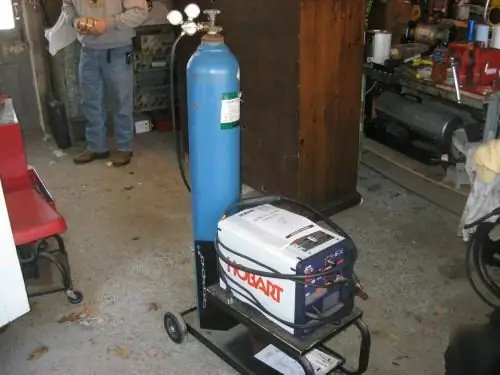
روش های جوشکاری و روکش نیمه اتوماتیک
روش بهینه برای کار با آلومینیوم و آلیاژهای مختلف غیرآهنی. به لطف تنظیم انعطاف پذیر پارامترهای تجهیزات و امکان استفاده از محیط های مختلف حفاظتی، اپراتور می تواند یک درز با کیفیت بالا روی قطعه کار تا ضخامت 12 میلی متر با قدرت جریان کم به دست آورد. روش نیمه اتوماتیک بازیابی قطعات با جوشکاری با استفاده از الکترودهای تنگستن به ضخامت 0.8-6 میلی متر انجام می شود. ولتاژ در این مورد می تواند از 20 تا 25 ولت متغیر باشد و قدرت جریان در 120 A است.
تکنولوژی بازیابی فشار جایگزین
علاوه بر روشهای حرارتی جوشکاری و روکشکاری، از گروه وسیعی از روشهای تماسی یا سرد تغییر ساختار بلنکهای فلزی نیز استفاده میشود. به طور خاص، ترمیم قطعات با جوشکاری تحت فشار با استفاده از واحدهای مکانیکی با پانچ انجام می شود. در فرآیند تغییر شکل پلاستیک، یک اتصال جوشی با پارامترهای خاص در نقاط تماس تشکیل می شود. پیکربندی اثر تغییر شکل به ویژگی های پانچ و تکنیک فشرده سازی بستگی دارد.

نتیجه گیری
امروزه هیچ راه موثرتری برای اصلاح عیوب سازه فلزی به جز جوشکاری و روکش وجود ندارد. نکته دیگر این است که در این بخشها، روشهای مختلف برای پیادهسازی فناوری در عمل توسعه فعالی دارد. امیدوار کننده ترین جهت را می توان ترمیم قطعات با جوشکاری و روکش روی تجهیزات خودکار نامید. مکانیزه شدن عملیات تعمیر، بهره وری فرآیند را افزایش می دهدارگونومی و سطح ایمنی برای جوشکار. در همان زمان، روش های جوشکاری آرگون-قوس با دقت بالا با اتصال رسانه های محافظ گاز در حال توسعه است. هنوز خیلی زود است که در مورد اتوماسیون کامل در این راستا صحبت کنیم، اما از نظر کیفیت نتیجه، این بخش پیشرفته است.
توصیه شده:
جوشپذیری فولاد: طبقهبندی. گروه های جوش پذیری فولادها
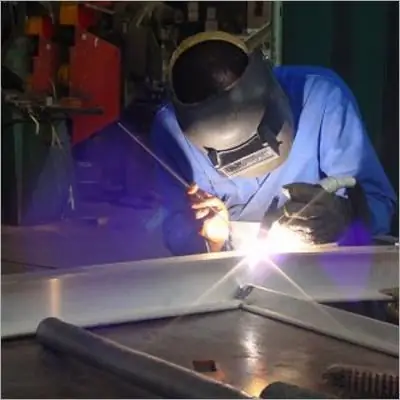
فولاد ماده اصلی ساختاری است. این یک آلیاژ آهن-کربن حاوی ناخالصی های مختلف است. تمام اجزای موجود در ترکیب آن بر خواص شمش تأثیر می گذارد. یکی از ویژگی های تکنولوژیکی فلزات، توانایی ایجاد اتصالات جوشی با کیفیت بالا است
تولید نجاری: ویژگی ها و فرآیند فن آوری
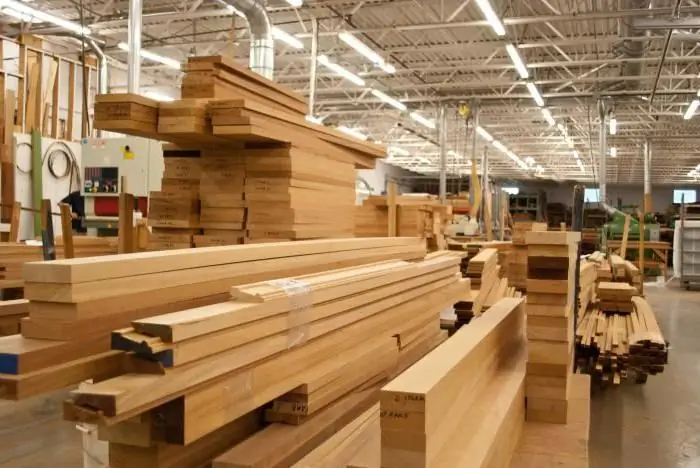
تولید نجاری مدرن شامل استفاده از تجهیزات پیشرفته برای تولید الوار با کیفیت بالا است
مهر و موم ورق قطعات: فن آوری ها و ویژگی های فرآیند
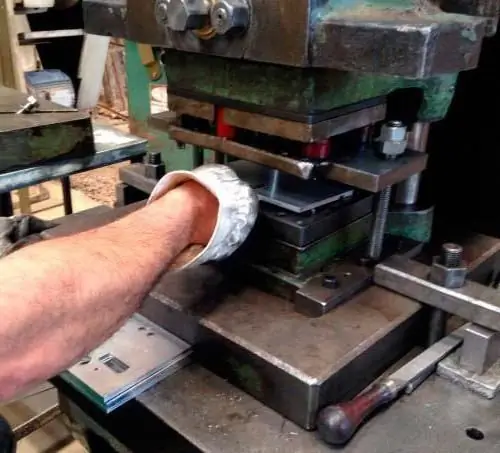
مقاله به مهر زنی ورق اختصاص داده شده است. ویژگی های این فرآیند، مزایای تکنولوژی، تجهیزات مورد استفاده و … در نظر گرفته شده است
قطعات آبکاری کروم. قطعات کروم در مسکو. قطعات کروم در سن پترزبورگ
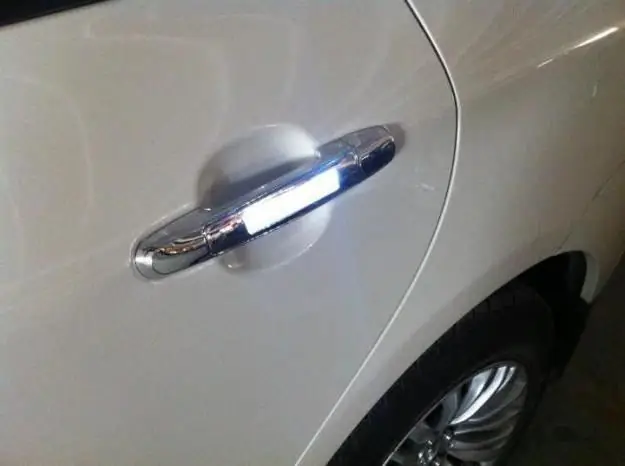
آبکاری کروم قطعات فرصتی است تا به آنها جان تازه ای بخشیده و آنها را قابل اعتمادتر و با کیفیت بالا در کارکرد
جوش لب به لب: تجهیزات، روشها و فناوری فرآیند
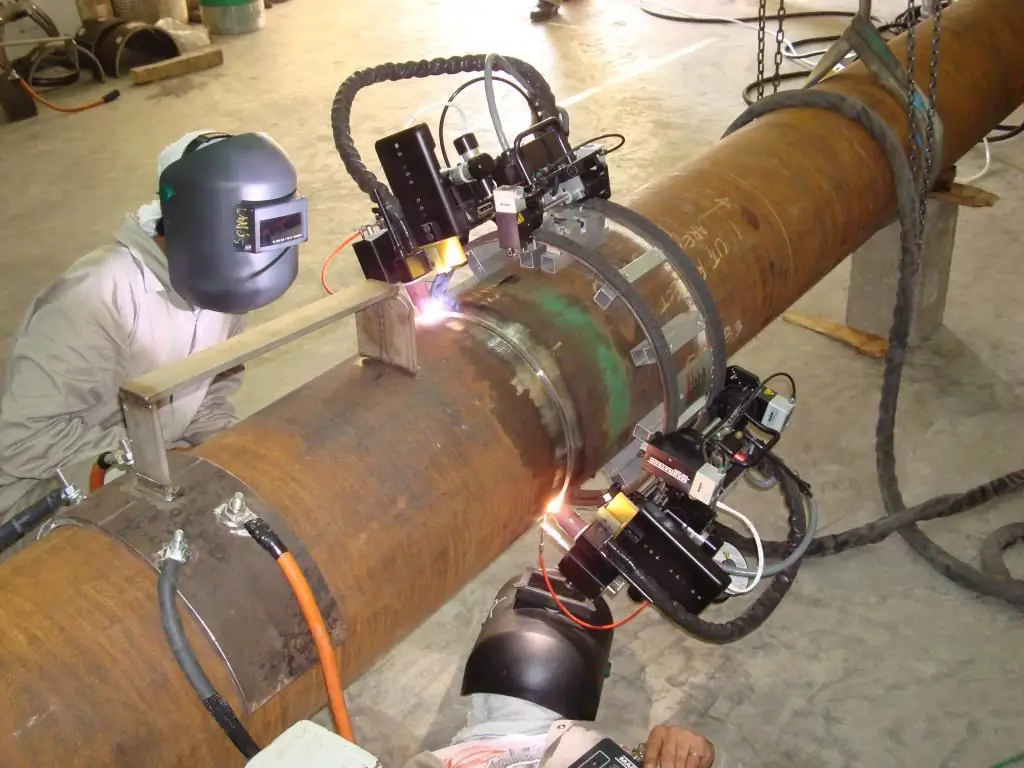
ویژگی های جوش لب به لب فلاش. انواع اتصالات جوش لب به لب و همچنین تجهیزات، روش ها و فناوری برای انجام فرآیند جوش لب به لب. عیوب درز جوش ناشی از جوش لب به لب و همچنین دلایل تشکیل آنها