2024 نویسنده: Howard Calhoun | [email protected]. آخرین اصلاح شده: 2023-12-17 10:25
رئیس هر بنگاه اقتصادی، صرف نظر از زمینه فعالیت، رویای این را دارد که سود رشد کند و هزینه های تولید بدون تغییر باقی بماند. سیستم "5S" در حال تولید (در نسخه انگلیسی 5S)، که تنها بر اساس استفاده منطقی از ذخایر داخلی است، به دستیابی به این نتیجه کمک می کند.
این سیستم از ابتدا ایجاد نشده است. چیزی مشابه در پایان قرن نوزدهم توسط فردریک تیلور آمریکایی پیشنهاد شد. در روسیه، این کار توسط دانشمند، انقلابی، فیلسوف و ایدئولوگ A. A. بوگدانوف که کتابی در مورد اصول مدیریت علمی در سال 1911 منتشر کرد. بر اساس مقررات مندرج در آن، اتحاد جماهیر شوروی NOT، یعنی سازمان علمی کار را معرفی کرد. اما کامل ترین سیستم 5C بود که توسط مهندس ژاپنی تایچی اوهنو پیشنهاد شد و توسط او در کارخانه تویوتا موتور در حال تولید معرفی شد. چیست و چرا سیستم ژاپنی تا این حد محبوب شده است؟
واقعیت این است که مبتنی بر یک اصل ساده است که نیازی به هزینه ندارد. عبارت است ازبعدی - هر کارمند، از نظافتچی گرفته تا مدیر، باید سهم خود را در گردش کار کلی تا حد امکان بهینه کند. این امر منجر به افزایش سود تولید در کل و افزایش درآمد همه کارکنان آن می شود. اکنون باتوم معرفی سیستم "5C" توسط شرکت ها در سراسر جهان از جمله روسیه انتخاب شده است. در این مقاله، ما سعی خواهیم کرد شکاکان را متقاعد کنیم که دانش ژاپنی واقعاً در هر زمینهای کار میکند.
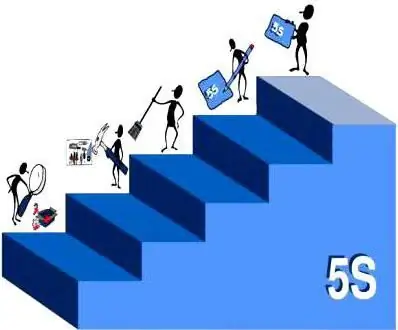
سیستم "5C" در حال تولید، چیست
International 5S مخفف پنج مرحله است («گام» در انگلیسی Step). برخی از اقتصاددانان و مروجین نگرش جدید به کار، نام را با پنج اصل ژاپنی توضیح می دهند که به طور مداوم در سیستم 5S اجرا می شوند: seiri، seiton، seiso، seiketsu و shitsuke. برای ما، "5C" های بومی ما نزدیک تر و قابل درک تر هستند - پنج مرحله متوالی که باید برای رسیدن به رونق تولید خود تکمیل شود. این است:
1. مرتب سازی.
2. حفظ نظم.
3. تمیز نگه داشتن.
4. استانداردسازی.
5. بهبود.
همانطور که می بینید، سیستم "5C" در تولید به هیچ چیز ماوراء طبیعی نیاز ندارد. شاید به همین دلیل است که هنوز می توان با بی اعتمادی و نگرش بیهوده نسبت به او روبرو شد.
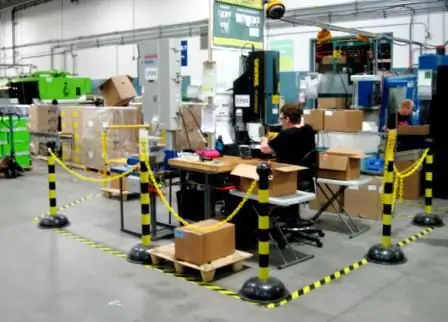
مراحل ایجاد سیستم
تایچی اوهنو خردمند ژاپنی که به لطف معرفی روشهای خود در کارخانه تویوتا، توانست ازمهندس به مدیر عامل، متوجه شد که چه تعداد زیان به دلیل ناهماهنگی ها و همپوشانی های مختلف رخ می دهد. مثلا چند پیچ کوچک به موقع روی نوار نقاله زده نشد و در نتیجه کل تولید متوقف شد. یا برعکس، قطعات با حاشیه عرضه میشد، زائد میشد و در نتیجه یکی از کارمندان مجبور میشد آنها را به انبار برگرداند، یعنی وقت خود را با کار خالی تلف میکردند. تایچی اوهنو مفهومی را توسعه داد که او آن را «در زمان مقرر» نامید. یعنی دقیقاً به تعداد قطعات مورد نیاز اکنون به نوار نقاله تحویل داده شد.
نمونه های دیگری می توان ارائه داد. سیستم "5S" در تولید همچنین شامل مفهوم "کانبان" بود که در ژاپنی به معنای "علامت تبلیغاتی" است. Taiichi Ohno پیشنهاد کرد که به هر قسمت یا هر ابزار یک برچسب به اصطلاح "kanban" وصل کنید که در آن تمام اطلاعات لازم در مورد قطعه یا ابزار داده می شود. اساساً برای هر چیزی صدق می کند. به عنوان مثال، به کالاها، داروها، پوشه ها در مطب. سومین مفهومی که سیستم 5S در تولید بر آن استوار است، مفهوم "کایزن" است که به معنای بهبود مستمر است. مفاهیم دیگری نیز تصور شد که فقط برای فرآیندهای تولید بسیار تخصصی مناسب بود. در این مقاله، آنها را در نظر نخواهیم گرفت. در نتیجه تمام نوآوری های آزمایش شده در عمل، 5 مرحله شکل گرفته است که برای هر تولیدی قابل اجرا است. بیایید آنها را با جزئیات تجزیه و تحلیل کنیم.
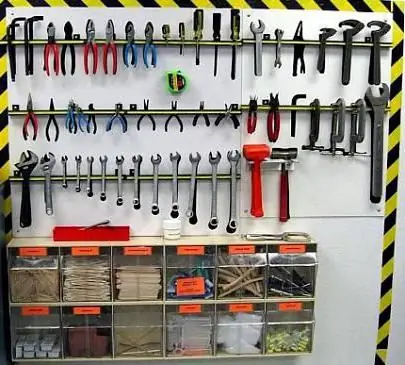
مرتبسازی
بسیاری از ما مواردی را روی دسکتاپ خود داریم که دراساسا مورد نیاز نیست به عنوان مثال، فرم های قدیمی، فایل های استفاده نشده، پیش نویس محاسبات، دستمال سفره ای که روی آن یک فنجان قهوه بود. و در میان این هرج و مرج ممکن است پرونده ها یا اسناد لازم وجود داشته باشد. اصول اولیه سیستم "5S" شامل بهینه سازی گردش کار شما است، یعنی اطمینان از اینکه زمان برای جستجوی چیزهای مناسب در میان آوار موارد غیر ضروری تلف نمی شود. این مرتب سازی است. یعنی در محل کار (نزدیک دستگاه، روی میز، در کارگاه - هر کجا)، همه اقلام در دو انبوه قرار می گیرند - ضروری و غیر ضروری که باید دور ریخته شوند. علاوه بر این، همه چیزهایی که نیاز دارید به توده های زیر تجزیه می شود: "اغلب و دائما استفاده می شود"، "به ندرت استفاده می شود"، "تقریبا استفاده نمی شود". این مرتبسازی را کامل میکند.
حفظ سفارش
اگر فقط اقلام را جدا کنید، معنایی نخواهد داشت. باید این اقلام (ابزار، اسناد) را به گونه ای چید که آنچه دائماً و غالباً استفاده می شود در معرض دید باشد یا به سرعت برداشته شود و به راحتی آن را برگرداند. چیزی که به ندرت استفاده می شود را می توان به جایی در جعبه فرستاد، اما باید یک تگ کانبان به آن وصل شود تا پس از مدتی به راحتی و با دقت پیدا شود. همانطور که می بینید، سیستم 5S در محیط کار با ساده ترین مراحل شروع می شود، اما در واقع بسیار موثر است. و علاوه بر این، روحیه و میل به کار را بهبود می بخشد.
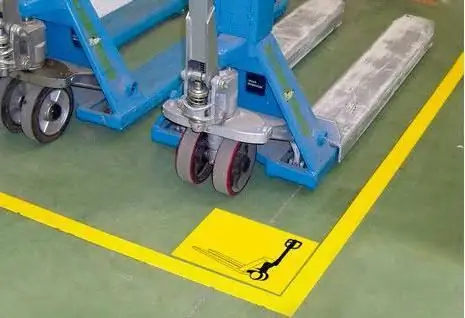
پاک نگه داشتن
این مرحله سوم برای بسیاری منطقیترین قدم است. از کودکی به ما یاد داده اند که پاک باشیم. دردر تولید نیز ضروری است و نه تنها میزهای کارمندان اداری یا کابینت ها در موسسات پذیرایی، بلکه ماشین آلات، اتاق های ابزار تمیز کننده نیز باید تمیز باشد. در ژاپن، کارمندان به خوبی از محل کار خود مراقبت می کنند، آنها را سه بار در روز تمیز می کنند - صبح قبل از کار، هنگام ناهار و عصر، در پایان روز کاری. علاوه بر این، شرکتهای آنها علامتگذاری ویژهای را برای مناطق معرفی کردهاند که به آنها امکان میدهد نظم را در تولید رعایت کنند، یعنی مناطقی از محصولات نهایی، ذخیرهسازی قطعات خاص و غیره با رنگهای مختلف مشخص میشوند.
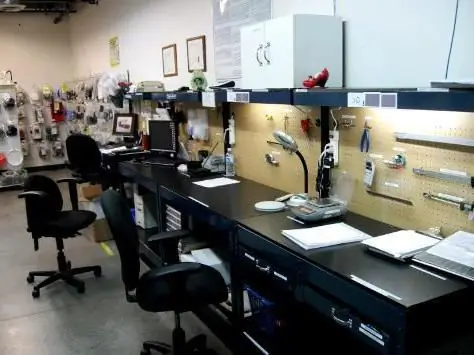
استانداردسازی
اصول استانداردسازی توسط تایچی اوهنو ابداع شد. آنها همچنین به طور گسترده توسط سیستم مدرن 5S استفاده می شوند. مدیریت تولید، به لطف استانداردسازی، ابزار فوق العاده ای برای کنترل تمام فرآیندها دریافت می کند. در نتیجه علل تاخیر از زمان بندی به سرعت از بین رفته و خطاهایی که منجر به عرضه محصولات بی کیفیت می شود اصلاح می شود. در کارخانه تویوتا موتور، استانداردسازی به این صورت بود: سرکارگرها برنامه های کاری روزانه را ترسیم کردند، دستورالعمل های دقیقی در محل کار ارسال شد و در پایان روز کاری، کارگران ویژه بررسی کردند که کدام انحراف از برنامه در طول روز و چرا اتفاق افتاده است. این قانون اساسی استانداردسازی است، یعنی دستورالعمل های دقیق، برنامه های کاری و کنترل بر اجرای آنها. اکنون بسیاری از شرکت ها، به عنوان مثال، کارخانه های ENSTO در استونی، یک سیستم پاداش را برای کارکنانی که به شدت از مفاد سیستم 5C پیروی می کنند و بر این اساس، بهره وری خود را افزایش می دهند، معرفی می کنند.انگیزه بزرگی برای اتخاذ این سیستم به عنوان یک روش زندگی است.
بهبود
گام پنجم که سیستم "5S" را در تولید کامل می کند، بر اساس مفهوم کایزن است. این بدان معناست که همه کارکنان صرف نظر از موقعیت شغلی خود باید برای بهبود روند کار در حوزه ای که به آنها سپرده شده است تلاش کنند. ماهیت فلسفی کایزن این است که کل زندگی ما هر روز بهتر می شود و از آنجایی که کار بخشی از زندگی است، نباید از پیشرفت ها نیز دور بماند.
حوزه فعالیت در اینجا گسترده است، زیرا کمال محدودیت ندارد. طبق مفاهيم ژاپني ها، خود كارگران بايد بخواهند فرآيند توليد خود را بدون دستور و اجبار بهبود بخشند. اکنون بسیاری از سازمانها در حال ایجاد تیمهایی از کارگران هستند که کیفیت محصول را نظارت میکنند، تجربیات مثبت خود را به دیگران آموزش میدهند و به دستیابی به برتری کمک میکنند.
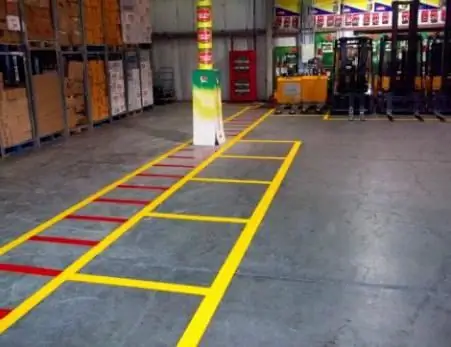
اشتباهات اساسی
برای اینکه سیستم "5C" شروع به کار کند، سازماندهی آن یا استخدام کارمندانی که همکاران خود را مجبور به اجرای آن کنند کافی نیست. مهم این است که مردم به سودمندی این نوآوری پی ببرند و آن را به عنوان یک سبک زندگی بپذیرند. معرفی سیستم "5S" در روسیه در تولید دقیقاً به دلیل تفاوت ذهنیت روسی ما با ژاپنی با مشکلاتی روبرو است. بسیاری از تولیدات ما با موارد زیر مشخص می شوند:
1. کارکنان، به خصوص اگر انگیزه ای برای آنها وجود نداشته باشد، به دنبال افزایش سود شرکت نیستند. آنها می پرسند،چرا سعی کنید رئیس را حتی ثروتمندتر کنید اگر او از قبل همه چیز دارد.
2. خود رهبران علاقه ای به معرفی سیستم «5S» ندارند، زیرا مصلحت را در آن نمی بینند.
3. بسیاری از دستورات "از بالا به پایین" عادت دارند فقط برای "تیک" اجرا شوند. در ژاپن نگرش کاملاً متفاوتی نسبت به کار آنها وجود دارد. به عنوان مثال، همان تایچی اوهنو، با معرفی سیستم "5S"، نه به سود شخصی، بلکه به سود شرکتی که در آن فقط یک مهندس بود فکر می کرد.
4. در بسیاری از شرکت ها، سیستم 5S به اجبار معرفی می شود. تولید ناب، که به معنای حذف زیانهای مختلف (زمان کار، مواد خام، کارکنان خوب، انگیزه و سایر شاخصها) است، کار نمیکند، زیرا کارگران شروع به مقاومت در برابر نوآوریها در سطح ناخودآگاه میکنند، که در نهایت تمام تلاشها را به صفر میرساند..
5. مدیرانی که این سیستم را پیادهسازی میکنند، ماهیت آن را کاملاً درک نمیکنند، که باعث شکست در فرآیندهای تولید ثابت میشود.
6. استانداردسازی اغلب به بوروکراسی تبدیل میشود، یک کار خوب مملو از دستورالعملها و دستورالعملهایی است که فقط در کار اختلال ایجاد میکنند.
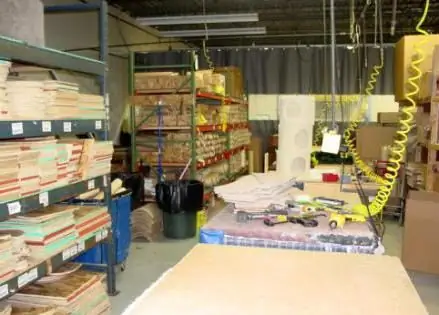
بررسی
روس هایی که سیستم "5S" را در تولید معرفی کرده اند، بازخورد در مورد این نوآوری بسیار مبهم است. نکات مثبت برجسته:
- در محل کار بودن بهتر است؛
- با چیزهای کوچک غیر ضروری از کار منحرف نشوید؛
- گردش کار واضح تر؛
- خستگی در پایان شیفت کاهش یافت؛
- اندکی افزایش یافته استحقوق با افزایش بهره وری نیروی کار؛
- صدمات شغلی کاهش یافت.
معایب ذکر شده:
- هنگام دسته بندی، همه چیز را مجبور می کنند دور بریزند؛
- استانداردسازی منجر به افزایش بوروکراسی شده است؛
- معرفی سیستم "5C" مشکلات را در همه حوزه های سازمانی تشدید نکرده است؛
- قرار دادن سیستم 5S در وهله اول مسائل مهمی مانند کمبود قطعات یدکی را تحت الشعاع قرار داده است.
توصیه شده:
سیستم هیدرولیک: محاسبه، طرح، دستگاه. انواع سیستم های هیدرولیک. تعمیر. سیستم های هیدرولیک و پنوماتیک
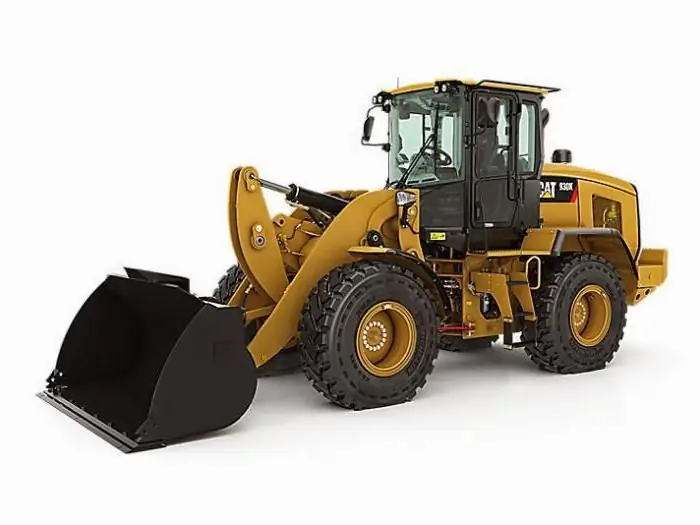
سیستم هیدرولیک دستگاه خاصی است که بر اساس اصل یک اهرم مایع کار می کند. چنین واحدهایی در سیستم های ترمز خودروها، بارگیری و تخلیه، ماشین آلات کشاورزی و حتی در صنعت هواپیماسازی استفاده می شوند
مدیریت متمرکز: سیستم، ساختار و عملکردها. اصول مدل مدیریت، مزایا و معایب سیستم
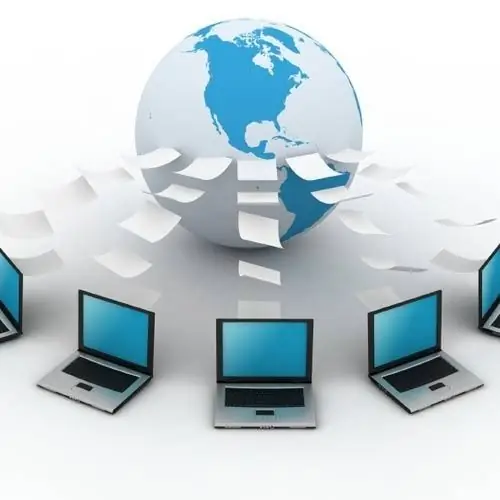
کدام مدل مدیریت بهتر است - متمرکز یا غیر متمرکز؟ اگر کسی در پاسخ به یکی از آنها اشاره کند، در مدیریت بلد نیست. زیرا در مدیریت الگوهای بد و خوب وجود ندارد. همه چیز به زمینه و تجزیه و تحلیل شایسته آن بستگی دارد، که به شما امکان می دهد بهترین راه را برای مدیریت شرکت در اینجا و اکنون انتخاب کنید. مدیریت متمرکز نمونه خوبی از این موضوع است
اصول ایجاد یک سیستم مالیاتی. سیستم مالیاتی فدراسیون روسیه
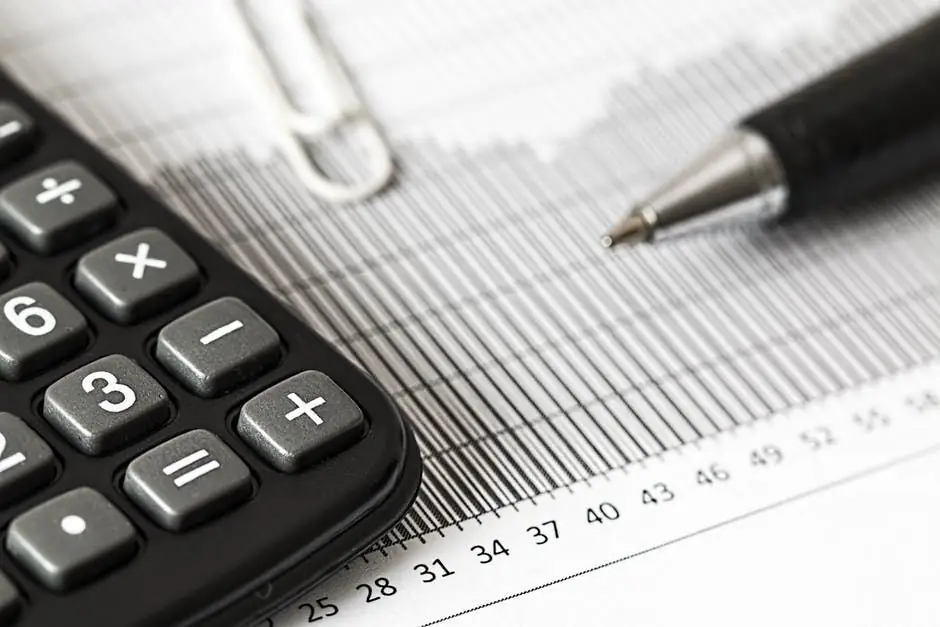
در سیستم مالیاتی، هر یک از عناصر آن - پرداخت کننده (شخص حقوقی یا حقیقی) موظف به پرداخت اجاره یا مالیات است. در این مقاله اصول ساختن یک سیستم مالیاتی یا نمونه هایی که باید در رابطه با مودیان مالیاتی و دولت اعمال شود، بررسی می شود
"Kanban"، سیستم تولید: توضیحات، ماهیت، عملکردها و بررسی ها
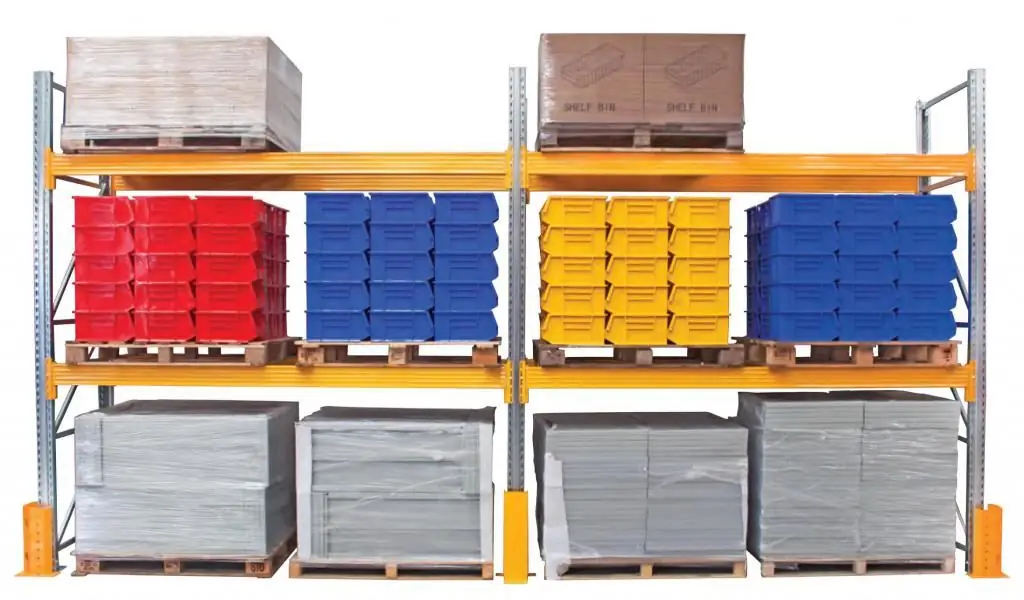
Kanban شناخته شده ترین روش مدیریت تولید صنعتی در مفهوم Just-in-Time است. با حداقل هزینه های سازمانی، می تواند زمان کار و هزینه منابع مادی را به میزان قابل توجهی کاهش دهد
سیستم پردازش: توضیحات، ویژگی ها. سیستم های پردازش در روسیه
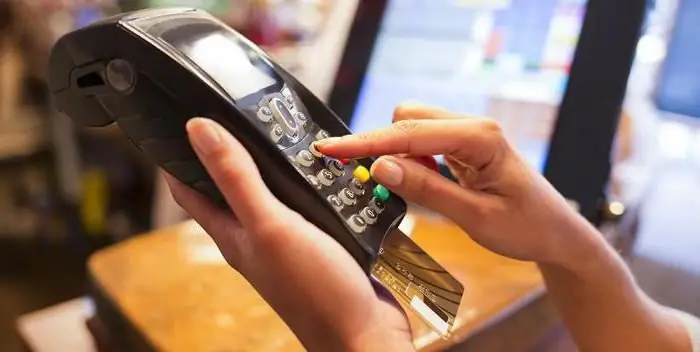
کارت های پلاستیکی جایگزین مناسبی برای پول نقد هستند. آنها جمع و جور، ایمن و آسان برای استفاده هستند. اما مکانیسم از قبل آشنا برای پرداخت کالا با کارت پلاستیکی به ندرت باعث می شود مردم به این فکر کنند که در هنگام تماس کارت بانکی با پایانه پرداخت چه فرآیندهایی انجام می شود. بنابراین، امروز در مورد سیستم های پردازش صحبت خواهیم کرد