2024 نویسنده: Howard Calhoun | [email protected]. آخرین اصلاح شده: 2023-12-17 10:25
توسعه علم و فناوری در دنیای مدرن مبتنی بر استفاده از رویه های خاص برای طراحی و نوسازی سازه های موجود، روش ها و رویکردهای مترقی در فعالیت های تولیدی است. راه حل های یکپارچه ای که توسعه مداوم طراحی و پایه فناوری شرکت های صنعتی و همچنین انطباق آنها با استفاده منطقی اقتصادی را تضمین می کند، آماده سازی فنی تولید نامیده می شود. این مبتنی بر فرآیندهای نوآورانه ای است که در زمینه تحقیقات علمی و مهندسی (طراحی و آماده سازی فناوری تولید) رخ می دهد.
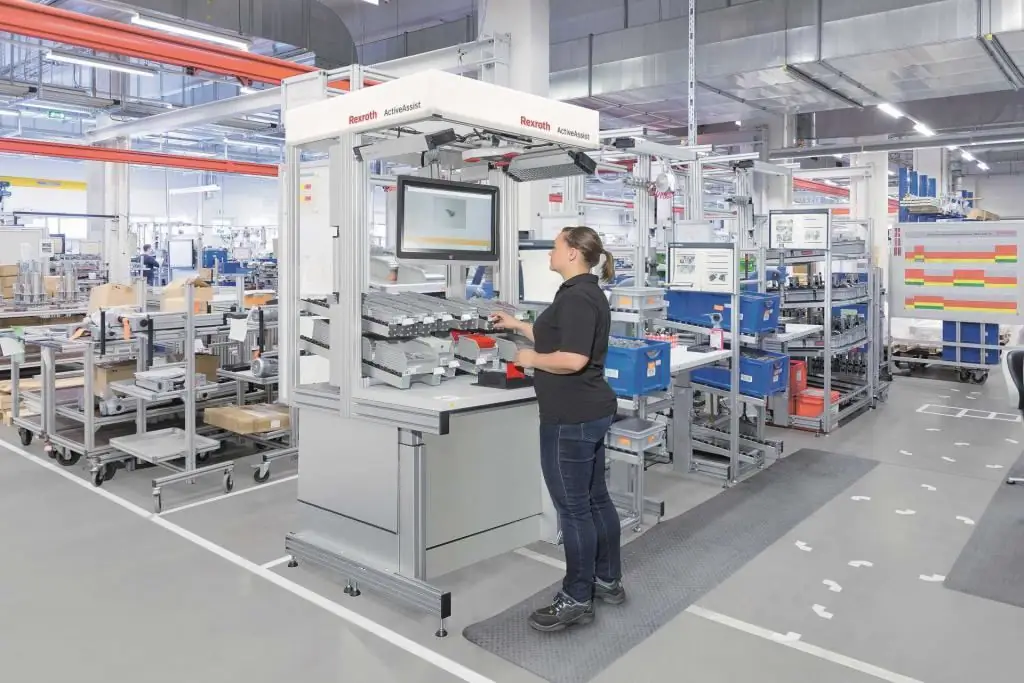
انواع مطالعات
تحقیقات علمی می تواند سطح رقابت پذیری محصولات توسعه یافته را به میزان قابل توجهی افزایش دهد. از منظر فرآیندها یا پدیده هایی که به سمت آنها سوق داده می شوند، آنها در چارچوب سه گروه اصلی در نظر گرفته می شوند:
- تحقیق پایه -دستیابی به قوانین یا الگوهای رفتاری جدید اشیاء و سیستم های واقعیت اطراف را با هدف استفاده بیشتر در تولید و فعالیت های اقتصادی افراد ممکن می سازد. توسط سازمان های تحقیقاتی ویژه (تخصصی) انجام می شود.
- تحقیق اکتشافی - آزمایش الگوهای باز برای فعالیتهای تولیدی، که امکان افزایش سطح علمی و فنی و کارایی کلی شرکتها و امکانات بخش عمران را فراهم میکند.
- کاربردی - در ادامه تحقیقات قبلی، آنها امکان حل مشکلات خاص علمی و مهندسی، ایجاد فناوری ها یا طرح های جدید را می دهند.
تحقیقات پایه معمولاً با بودجه دولتی تأمین می شود زیرا اغلب ارزش بازاری ندارند. جستجو و تحقیقات کاربردی با هدف حل مشکلات عملی انجام می شود و اغلب توسط شرکت های تجاری تامین مالی می شود. تحقیقات علمی در مورد یک مشکل خاص که بر اساس یک برنامه خاص انجام می شود، موضوع علمی (اقتصادی - قراردادی) نامیده می شود.
به عنوان یک قاعده، پیش تولید طراحی شامل انواع خاصی از تحقیقات است.
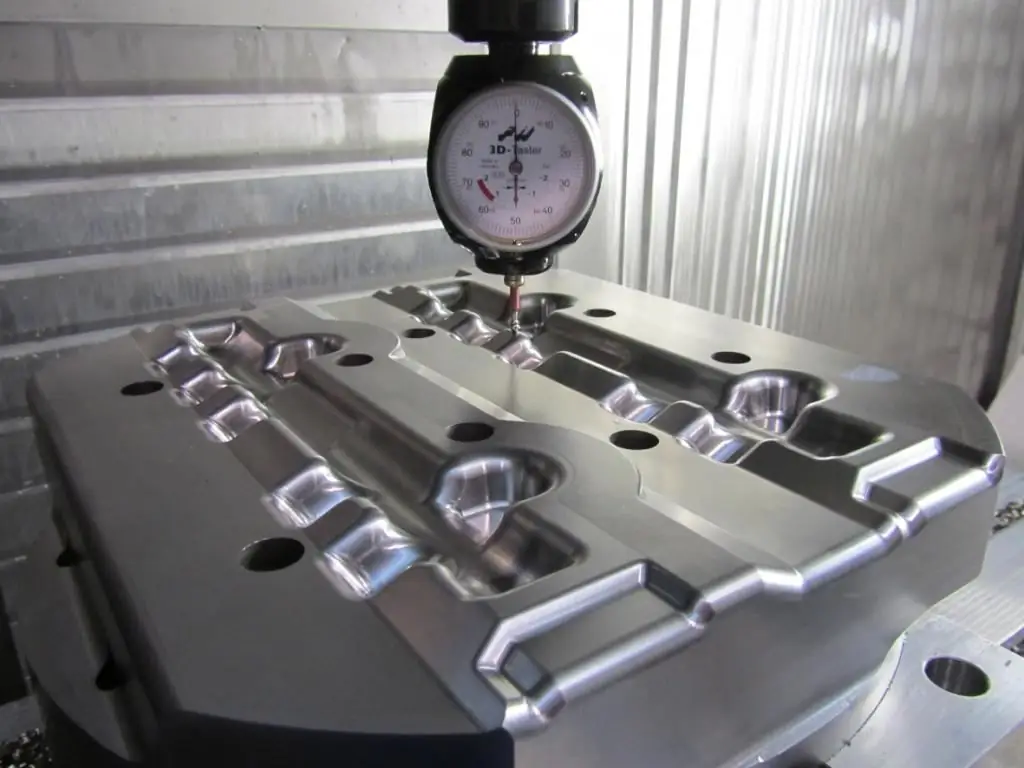
مراحل اجرای موضوع علمی
اقتصادی-قراردادی، یعنی توسط شرکت های فردی تامین مالی می شود، و تحقیقات علمی طبق یک طرح سنتی خاص انجام می شود:
- تدوین شرایط مرجع برای حل مشکل و امکان سنجی موضوع پیشنهادی؛
- انتخاب جهت تحقیق، که بر اساسمطالعه راه حل های موجود، تحقیق در مورد اطلاعات ثبت اختراع، و توسعه دستورالعمل های اجرایی عمومی؛
- انجام تحقیق (نظری و تجربی) برای تعیین موقعیت های نظری داده های واقعی به دست آمده از آزمایش؛
- نتیجه گیری کلی در مورد کار انجام شده و تهیه گزارش.
نتایج به دست آمده مبنایی برای مراحل بعدی آماده سازی طراحی برای تولید است. یک شرکت صنعتی که بخشهایی را برای طراحی و توسعه فناوریهای جدید (طراح ارشد، فنشناس ارشد) در ساختار سازمانی خود ایجاد کرده است، میتواند به طور مستقل این مطالعات را انجام دهد. در صورت لزوم، امکان جذب سازمانهای تحقیقاتی خارجی (موسسات، شرکتهای سرمایهگذاری) وجود دارد که این امر باعث میشود تا پیچیدگی کار انجام شده افزایش یابد و سرعت مراحل جداگانه افزایش یابد.
تحقیقات انجام شده (فرآیندهای نوآورانه) به شما امکان می دهد سه نوع اصلی نوآوری - کشف، اختراع و پیشنهاد منطقی را دریافت کنید. ورود آنها به تولید و فعالیت های اقتصادی عنصر مهمی در توسعه فنی بنگاه ها در طول زمان بوده و یکی از عناصر کلیدی در سازماندهی طراحی و آماده سازی فناورانه تولید می باشد.
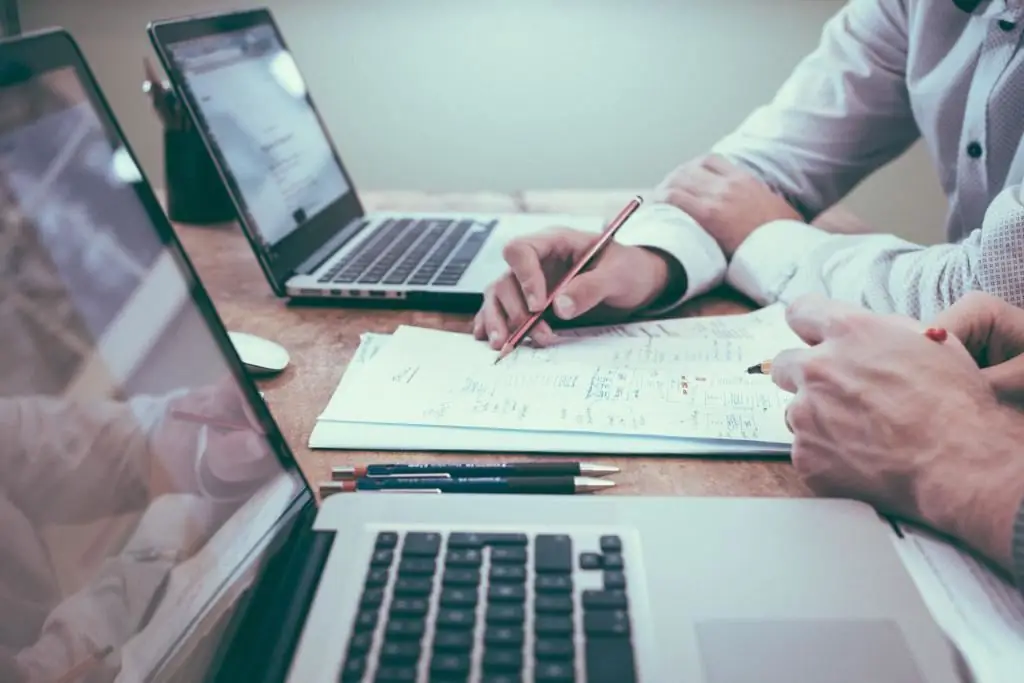
مسائل کلی سازمان
در فرآیند فعالیت، بنگاه های صنعتی نیاز به بازسازی مستمر ساختمان های صنعتی، تجهیزات تکنولوژیکی وعناصر زیرساخت (جریان ترافیک، شبکه های مهندسی، ارتباطات و غیره) به دلیل زوال فیزیکی. علاوه بر این، لازم است از توسعه فناوری و فناوری شرکت برای برآوردن شرایط جدید اقتصادی و نیازهای روزافزون مصرف کنندگان اطمینان حاصل شود. که هدف اصلی پیش تولید طراحی است.
سطح واقعی وضعیت فنی شرکت باید در فواصل زمانی مشخص با در نظر گرفتن تعدادی از شاخص های سیستم تولید ارزیابی شود. آنها در پویایی تغییرات در طول زمان هم در خود شرکت و هم در سیستم های مرتبط ارزیابی می شوند که اصلاح منطقی آنها را امکان پذیر می کند. لازم به ذکر است که کنترل وجوه بنگاه ها و حفظ آنها در شرایط کاری وظیفه اصلی فعالیت تاسیسات زیربنایی بنگاه ها می باشد.
پارامترهای ارزیابی توسعه
به عنوان یک قاعده، شاخص ها بر اساس معیارهای خاصی در نظر گرفته می شوند:
- سطح تجهیزات فنی - نحوه تأمین بودجه (وجوه) و منابع انرژی لازم برای کارگران تولیدی.
- درجه جدید بودن فناوری ها - توزیع متناسب فرآیندها بر اساس شدت کار، درصد فرآیندها و تکنیک های جدید فناوری، میانگین سن عناصر فناوری مورد استفاده، منطقی بودن استفاده از مواد و قطعات یدکی.
- تازگی و انطباق ویژگی های تجهیزات - پارامترهای عملکرد، عملکرد، مصرف مواد، شاخص های قابلیت اطمینان (قابلیت اطمینان، دوام، قابلیت نگهداری وایمنی)، میانگین مدت کارکرد، درصد تجهیزات پیشرونده، درصد تجهیزاتی که از نظر فیزیکی و اخلاقی فرسوده شده اند.
- شاخص های مکانیزاسیون (اتوماسیون) - تعداد عملیات مکانیزه کار؛ درصد محصولات تولید شده با استفاده از دستگاه های خودکار (فناوری).
سیستم آماده سازی طراحی تولید به شما امکان می دهد ارزش این شاخص ها را در محدوده تعیین شده حفظ کنید.
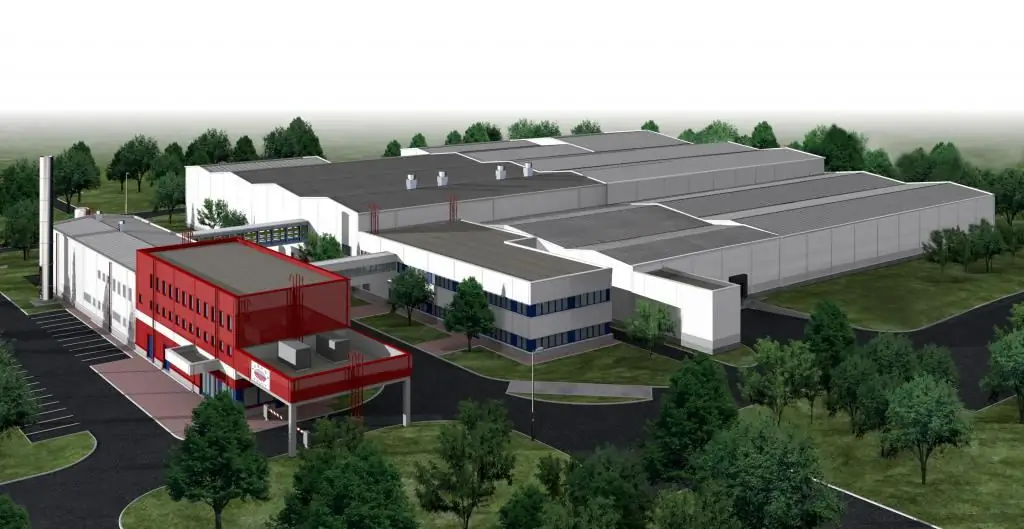
جهت توسعه فناوری
برای حل مشکلات فوری حفظ و بهبود سیستمهای تولید در طول زمان، مکانیسمها و رویههای مختلفی برای تأثیرگذاری بر عناصر شرکت استفاده میشود. برای اجرای آنها، رویکردهای آماده سازی طراحی تولید درگیر است. این مقاصد عبارتند از:
- ساخت تاسیسات جدید - ساخت بنگاه از صفر، ایجاد واحد تولیدی جدید (کارگاه، سایت) به ترتیب مقرر در قانون.
- افزایش مقیاس شرکت موجود - معرفی ظرفیتهای اضافی بنگاه از طریق ایجاد بخشها یا تسهیلات اضافی. افزایش ردپای واحدهای موجود برای بهبود عملکرد تولید، ظرفیت افزایش جریان محصول و کارایی هزینه.
- بازسازی - تغییر زیرسیستم های فردی شرکت، بهبود ساختارهای فنی و فنی. این بر اساس جایگزینی تجهیزات تکنولوژیکی منسوخ و افزایش سهم انجام می شودفرآیندهای مکانیزه (اتوماتیک)، حذف عدم تناسب در کار زیرسیستم های مختلف شرکت (که به بهبود شاخص های کلان اقتصادی شرکت کمک می کند).
- تجهیز مجدد یا تجهیز مجدد وسایل تولید - جایگزینی تجهیزات و ابزار منسوخ شده با تجهیزات پیشرفته تر با عملکرد بهبود یافته.
- مدرنسازی - بهبودهای فردی در عناصر سیستم تولید (تجهیزات، فناوری، سازمان و کنترل) برای تطبیق تولید و محصولات ایجاد شده (عناصر، سیستمها) با شرایط متغیر بازار، استانداردها یا نیازهای مصرفکننده..
علاوه بر این شاخصها، سیستمهای تولید بر اساس تأثیرات زیستمحیطیشان ارزیابی میشوند. آنها مقیاس بازیافت زباله های تولیدی، آلودگی محیط طبیعی، درصد محصولات سازگار با محیط زیست را در نظر می گیرند.
سازمان آماده سازی طراحی تولید
کار پژوهشی در زمینه طراحی سازه های پیشرفته فرآیندی پرزحمت، مقیاس بزرگ و پرمشقت از نظر استفاده از منابع مادی و مالی است که نتایج حاصل از طراحی محصولات جدید را با ارزیابی تجربی بعدی ترکیب می کند. آنها تحت کنترل OGK (بخش طراح اصلی) یا دفتر طراحی (KB) بخش فنی شرکت انجام می شوند.
در نتیجه پیشرفت های مداوم، پارامترهای مختلف سیستم های تولید بهبود می یابد - بهره وری و عملکرد افزایش می یابد، هزینه بهینه می شود، فواصل زمانی تولید تغییر می کند وشرایط برای کارآمدترین عملکرد واحدهای تولیدی.
نقش مهمی در سازماندهی آماده سازی طراحی تولید به بخش های طراحی شرکت داده می شود. نظم خاصی برای ذخیره سازی نقشه ها، نقشه ها و نمودارها ایجاد می شود. سازوکارهایی برای ارائه به موقع آنها به واحدهای تولیدی در حال توسعه است. طراحی دقیق و نظم فنی حفظ شده است.
مشکلات آماده سازی طراحی تولید
سوالات اساسی که هنگام طراحی سیستم های ساده و پیچیده حل می شوند عبارتند از:
- تجزیه و تحلیل شرایط فنی برای عناصر سازه ای که در ویژگی های ساخت و تعمیر منعکس شده است؛
- توسعه پروژه های مختلف برای محصولات مورد نظر با هدف بهبود طرح های کلی طراحی؛
- توسعه تلرانس تعمیرات (افزایش قابلیت تعویض قطعات و کاهش هزینه های تولید)؛
- بهبود و نوسازی پایه عنصر؛
- یکسان سازی مجموعه ها (مجموعه ها، قطعات) برای حذف تخمین بیش از حد غیر منطقی تعداد اندازه های استاندارد.
همانطور که می بینید، استفاده از پیش تولید طراحی مستقیماً بر سطح ضرر و زیان در طول عملیات بعدی تأسیسات تأثیر می گذارد.
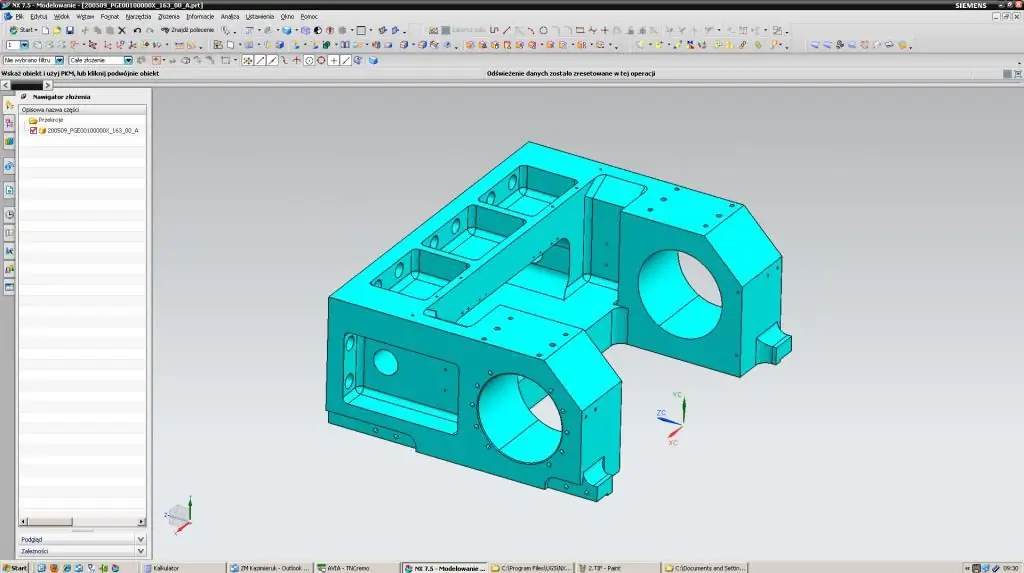
مجموعه مقالات
محتوای مطالعات طراحی با توجه به ویژگی های مشخصه موضوع مطالعه، هدف عملکردی آن و روش ساخت (تعمیر) تعیین می شود. به طور کلی، چندین وجود داردمراحل معمولی که نتیجه آن ایجاد اسناد نظارتی و فنی خواهد بود. آنها طبق ESKD انجام می شوند. پیچیدگی محصول و دامنه استفاده بیشتر از آن تأثیر مستقیمی بر محتوا و تعداد مراحل دارد. بنابراین، برخی از آنها، به ویژه مراحل آماده سازی، ممکن است کاهش یافته، ترکیب شوند یا به طور کامل وجود نداشته باشند.
مراحل پیش تولید طراحی:
- تنظیم شرایط مرجع (به اختصار TK). تهیه فهرستی از مراجع، تجزیه و تحلیل ادبیات خاص و اسناد نظارتی - دستورالعمل ها، دستورات، توضیحات و توصیه ها. تجزیه و تحلیل و تایید بعدی موارد تکلیف برای طراحی سازه. توسعه برنامه زمانبندی کار پیشنهادی در قالب یک مدل الگوریتمی (نمودار گانت یا نمودار شبکه). حسابداری برای هزینه های طراحی آینده محاسبه اولیه اثر اقتصادی از نتایج فعالیت نوآوری.
- توسعه یک پیشنهاد فنی (مشابه TP). محاسبه کامل مولفه های اقتصادی. در نظر گرفتن گزینه های طراحی و انتخاب بهینه ترین. تنظیم تعداد کل آثار و مدت زمان اجرا.
- اجرای طرح پیش نویس. در نظر گرفتن نمودارهای شماتیک طرح ها یا فرآیندهای جدید، انجام محاسبات اولیه ریاضی، تعیین ابعاد کلی محصول بر روی نقشه های کلی، ایجاد طرح و آزمایش آن؛
- طراحی فنی. زمان برترین و طولانی ترین مرحله تحقیق. انجام محاسبات اولیه برای استحکام سازه، قابلیت اطمینانو امنیت آزمایش نمونه اولیه (اجباری و/یا تسریع شده). نوسازی سازه بر اساس پارامترهای محاسبه شده. زمانبرترین، طولانیترین و گرانترین مرحله.
- تهیه اسناد کاری - ایجاد نقشه های مونتاژ، جزئیات محصول، ترسیم نمودارهای شماتیک و سیم کشی. ایجاد نسخه های تکراری و کپی از اسناد. طراحی نهایی.
مراحل پیش تولید طراحی به شما امکان می دهد چرخه کامل توسعه و اجرای مستندات پروژه را تکمیل کنید.
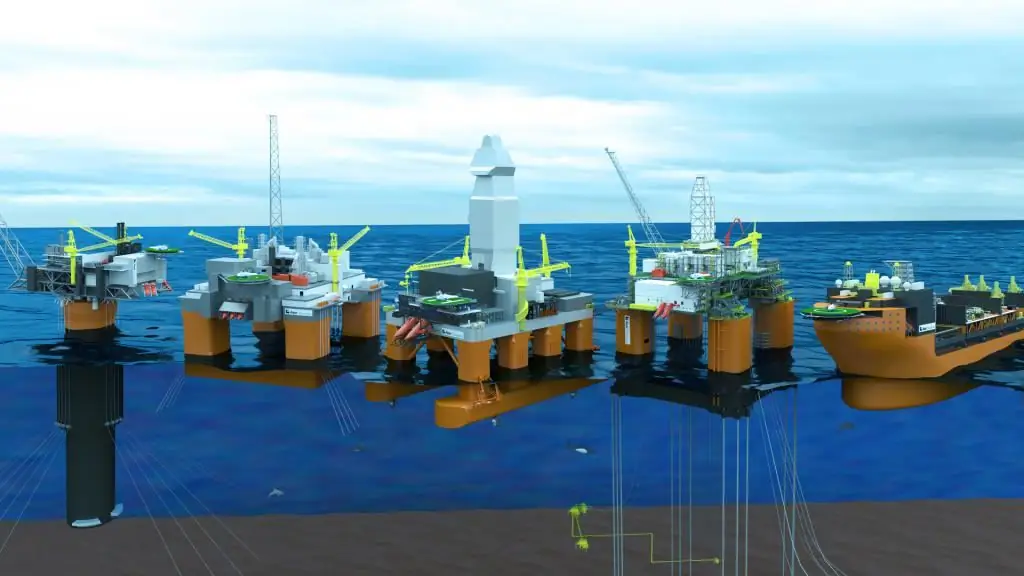
ویژگی های طراحی مدرن
به منظور برآوردن نیازهای روزافزون پایه المان سازه ها از نظر قابلیت اطمینان و کارایی محصولات صنعتی، در سال های اخیر، آماده سازی طراحی برای تولید با استفاده از سیستم های طراحی به کمک کامپیوتر صورت گرفته است. با توجه به افزایش پیچیدگی پروژه های فردی (به عنوان مثال، توسعه مدارهای مجتمع)، استفاده از روش های ماشینی خاص اغلب تنها راه ممکن برای ایجاد محصول مورد نظر با پارامترهای داده شده است.
هنگام خودکارسازی فرآیندهای طراحی، یک محصول بر اساس الگوریتم های ماشینی دقیق تعبیه شده در بسته های نرم افزاری تخصصی ایجاد می شود. این امر تأثیر عامل انسانی را بر دقت محاسبات و انتخاب مناسب ترین گزینه طراحی کاهش می دهد. به طور قابل توجهی زمان اجرای پروژه، آزمایش و هزینه های کل را در تمام مراحل طراحی کاهش می دهد.
طراحی-آماده سازی طراحی تولید در عین حال دارای چندین مزیت است که در عوامل زیر بیان می شود:
- به طور قابل توجهی پیچیدگی و مدت پروژه را کاهش می دهد؛
- هزینه های حقوق و دستمزد در حال کاهش است (به دلیل بهینه سازی کارکنان)؛
- سطح کیفیت محصول نهایی را افزایش می دهد؛
- شاخصهای قابلیت اطمینان در حال عادی شدن هستند؛
- انباشت راه حل های اثبات شده در پایگاه های داده صنعت؛
- اسناد به طور مداوم نظارت می شود؛
- مدلسازی ریاضی طرحهای غیربهینه و غیره را به حداقل میرساند.
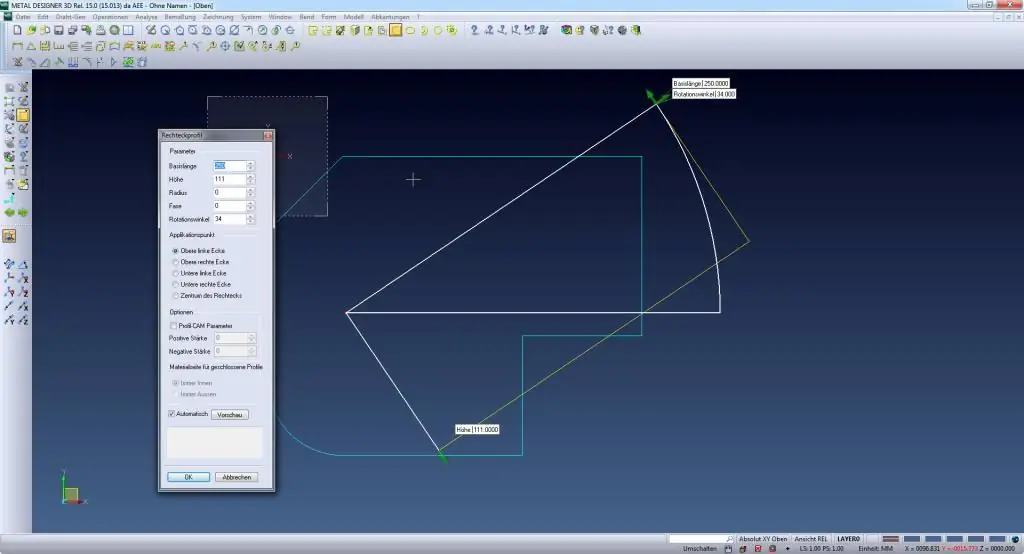
نتیجه گیری
سیستم آماده سازی طراحی تولید، حلقه ای ضروری در زنجیره چرخه عمر هر محصول است. هم برای ایجاد محصولات صنعتی و هم برای سیستم های تخصصی پیچیده با موفقیت یکسان استفاده می شود. همانطور که تجربه سال های اخیر نشان می دهد، اطلاعات روزافزون فرآیندهای تولید نیز الزامات جدیدی را برای بهبود سیستم های طراحی مطرح می کند.
توصیه شده:
دوغاب سیمان: خواص، قوانین آماده سازی، ترکیب، انطباق با الزامات GOST، هدف و کاربرد
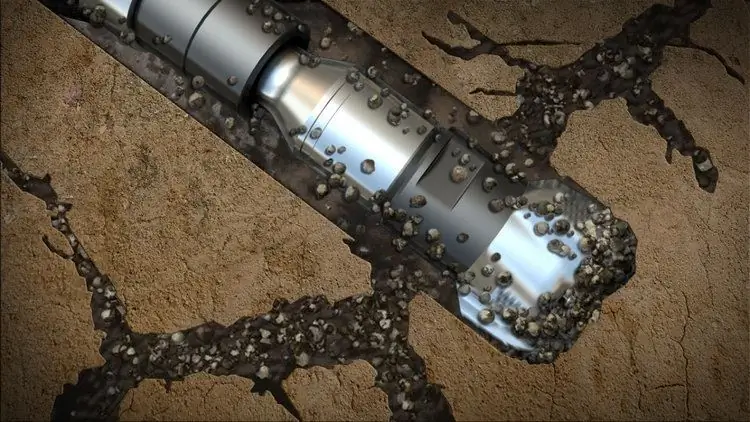
در طول فرآیند حفاری، از محلولهای ویژه برای خارج کردن قلمهها و محصولات حاصل از توسعه سنگهای محلی استفاده میشود. این عملیات برای افزایش کارایی ضربه مکانیکی دکل حفاری و پاکسازی سوراخ کف ضروری است. شستشو با استفاده از دوغاب سیمان انجام می شود که با استفاده از فناوری های ویژه تهیه می شود
تهیه اجناس برای فروش. انواع و هدف کالا. آماده سازی پیش فروش
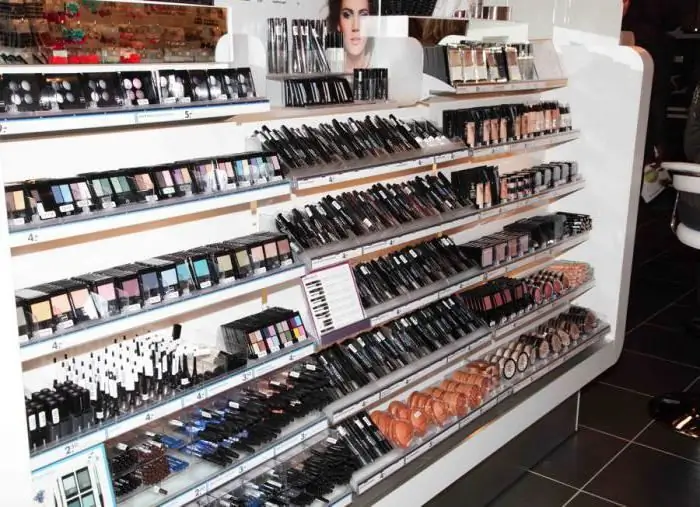
آماده سازی کالا برای فروش شامل طیف وسیعی از اقدامات لازم برای گردش سریع و افزایش سود خروجی است
آماده سازی فنی تولید: وظایف، مراحل، فرآیند و مدیریت
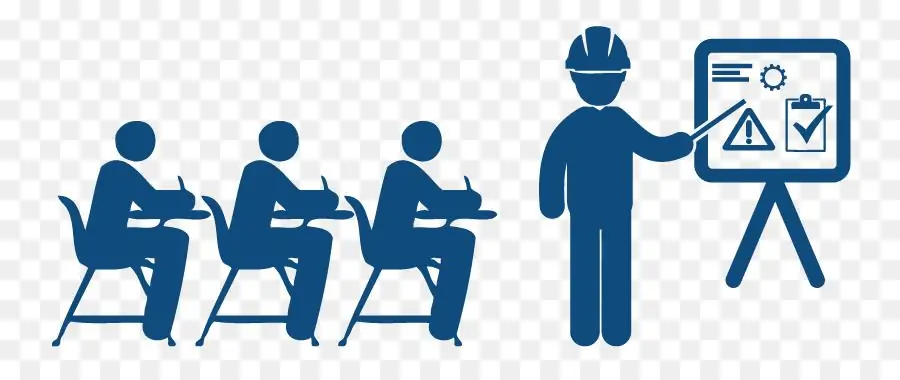
توسعه محصولات جدید، بسیار کارآمد و پیشرفته تر، رقابت پذیری در بازار جهانی - همه اینها مستقیماً با مسائل سازمانی مرتبط است که در میان آنها آماده سازی فنی تولید جایگاه ویژه ای را اشغال می کند. چرا او چنین نقشی دارد؟
عملکرد کدو تنبل در هر هکتار. ذخیره سازی و آماده سازی
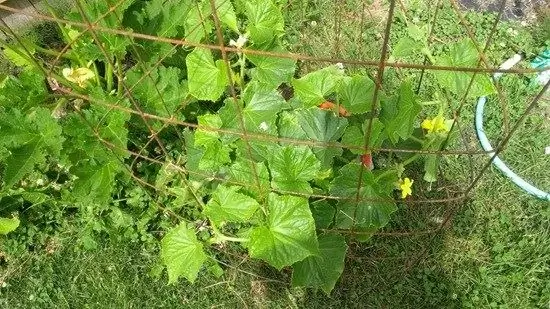
کدو تنبل یک سبزی بسیار محبوب در بین باغداران خانگی است. برداشت این محصول در یک منطقه حومه شهر، حتی در نامساعدترین سال، قابل برداشت بسیار زیاد است. در عین حال، میوه های کدو تنبل را می توان تا بهار به صورت تازه نگهداری کرد
آماده کردن پیاز برای کاشت روی سر. آماده سازی مجموعه های پیاز قبل از کاشت. آماده سازی خاک برای کاشت پیاز در بهار
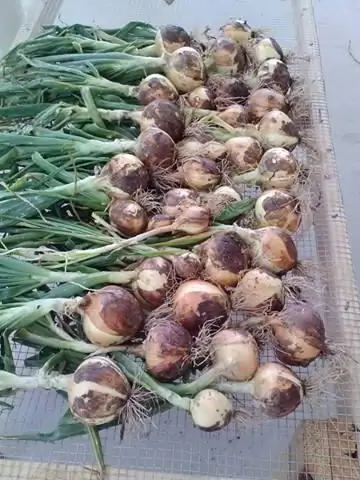
هر کدام از زنان خانه دار می دانند که همیشه باید پیاز در خانه باشد. این محصول تقریباً به هر غذایی اضافه می شود، می تواند فواید زیادی برای بدن ما به همراه داشته باشد